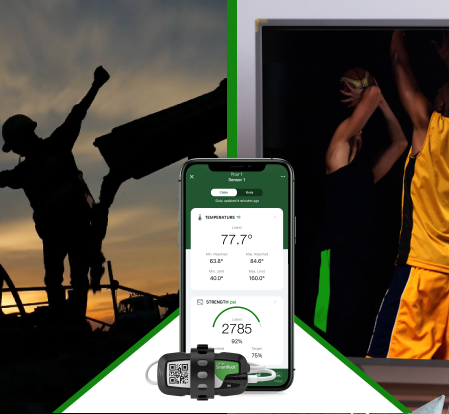
Got the game on? Don't miss a shot with SmartRock® in hand.
Concrete has compressive strength, meaning that it can withstand its own weight within a structure. However, it lacks tensile strength. Therefore, as soon as everyday loads are added to that structure, such as vehicles in a car park or on a bridge, it struggles under the additional weight due to a lack of flexibility. This leads to cracking and weakening of the structure. This is why steel reinforcing bars, or rebar, are embedded in the concrete. However, the rebar only provides passive reinforcement, meaning it does not bear any load or force until the concrete has already cracked. This is where post-tensioning comes in to provide additional active reinforcement.
What Is Post-Tensioning?
Post-tensioning (ACI 423) has gained significant popularity over the past 30 years, especially in modern high-rise buildings, industrial floors, and residential structures. Today, this technique is used extensively for slabs that cover a large surface area, such as tennis courts or parking lots. Compression is a force that squeezes or crushes, and tension is a force that pulls something apart. The purpose of post-tensioning is to place the concrete structure under compression in those regions where load causes tensile stress. Post-tensioning offsets this tensile stress.
Once the concrete has reached a specific initial compressive strength, but before the service loads are applied, the cables, or tendons, are pulled tight and tensioned then anchored to the outer edges of the concrete, thus maintaining the force in the strand for the life of the structure. The tensioning of the tendons is achieved by using a hydraulic jack. The result is a stiffer concrete slab that actively is compressed and has more capacity to resist tensile forces.
Read more about post-tensioning, including this technique’s disadvantages and advantages.
What Is Cold Weather Concreting?
- Concrete temperatures must be maintained higher than 40°F (4°C) for 48 hours after a pour.
- All concrete surfaces must be protected within the first 24 hours after being placed to prevent freeze damage.
- Concrete temperature cannot reach freezing levels before reaching a specific strength (3.5 MPa/500 psi) or the overall structure will have a reduced strength.
If these practices are not followed, any concrete construction project is subject to various risks. These include cracking, rapid temperature changes, and loss of durability.
Click here for more information about cold weather concreting.
Monitoring Concrete Temperature and Strength to Post-Tension in Cold Weather
When using post-tensioning in a construction project, temperature and strength of your in-situ concrete elements must be closely monitored. This is especially important in cold weather as concrete gains strength much more slowly in lower temperatures. Ensuring you have reached the required strength allows you to tension without any worries. If tensioning occurs too early, concrete is subject to cracking and, in extreme cases, the concrete must be ripped out entirely.
The most common method for monitoring the strength of in-situ concrete is the use of field-cured cylinders according to ASTM C31. However, when pouring in cold weather, ACI 306 specifically recommends not using this method as field-cured cylinders “can cause confusion and unnecessary delays in construction.” This is largely because it makes it difficult to maintain cylinders in the same conditions as your structure. It is, therefore, recommended that other in-place testing methods, like the maturity method, be used for monitoring concrete strength.
What Is Concrete Maturity?
The maturity method or ASTM C1074: Standard Practice for Estimating Concrete Strength by the Maturity Method, is a non-destructive testing technique. This method allows you to estimate the early-age and compressive strength of in-place concrete in real-time. It is based on the principle that concrete strength is directly related to its hydration temperature history. In other words, maturity is a value that represents the progression of concrete curing. A mix calibration is required to implement this concept in a project. The goal of the calibration is to determine a relationship between maturity and strength for a specific mix.
With Giatec’s free SmartRock app, you can share concrete temperature and strength results with the simple click of a button. This method allows you to eliminate field-cured cylinder testing and switch to wireless sensors for both temperature and strength monitoring. Wireless sensors, like SmartRock® are placed within the concrete formwork, secured on the rebar, before pouring. Temperature data is collected by the sensor and uploaded to any smart device within an app using a wireless connection. Our newest version of SmartRock includes an increased wireless signal range of up to 40 ft (12 m), which increases efficiency and saves time. There is no need to life heavy heating blankets to collect data from a wired sensor. Also, you will be notified right away if the temperature of your in-situ concrete has dropped too low.
The new SmartRock sensor also includes dual temperature monitoring for easy temperature differential analysis, which is particularly useful in cold weather concreting. This is because a concrete pour generates heat, which gets trapped in the core of the concrete. Meanwhile, the surface of the concrete will cool down rapidly due to the cold weather, causing a temperature differential. These opposing forces create tension in the slab, which can lead to cracking. Being able to check these two temperatures in real time allows you to make quick adjustments to keep the concrete at a safe temperature.
The information SmartRock collects is then used to calculate the compressive strength of the in-situ concrete element based on the maturity equation that is set up in the app. This strength data is considered to be very accurate and reliable as the sensors are subject to the same curing conditions as the in-situ concrete slab.
Equipped with real-time results, contractors can improve the heating process, decrease energy costs, and save time in their project schedule by knowing when to move on to subsequent construction operations, such as; formwork removal or post-tensioning.
The Problem of Tendon Deterioration
One of the biggest worries when tensioning is the possibility of corrosion. Though post-tensioned tendons are encased in protective materials, water and salts can still get in if the anchors of the steel tendons are not properly protected. This problem becomes more severe in cold weather conditions when de-icing salts are used and more moisture is in the air. The acceleration of corrosion results in a reduced service life of the structure.
Repair, Rehabilitation, & Strengthening of Tendons
The strength and serviceability of a structure that has experienced deterioration can be difficult to repair. External post-tensioning can be used to increase and/or restore the load capacity of the structure. This can be done using steel or concrete beams. Repairs should be performed as required to maintain the structure and assure it is in a safe and serviceable condition. The most effective way to manage deterioration of a structure is to keep up with its maintenance. This includes practices to limit moisture and ensure adequate drainage and waterproofing by protecting expansion joints and seals. Furthermore, replacing deteriorated grout plugs and implementing protocols to prevent mechanical damage to tendons ensures the longevity of the structure. If deterioration has already begun in the post-tensioned structure, techniques such as tendon drying, re-greasing, injecting with an epoxy resin, and cathodic protection of anchorages can be introduced to limit further progression.
**Editor’s Note: This post was originally published on October 15, 2019, and has been updated for accuracy and comprehensiveness.