Mass Concrete and its Relationship With Temperature
Mass concrete pours are becoming more and more present in the construction industry. As our ambition grows, the size of our concrete structures grow with it.
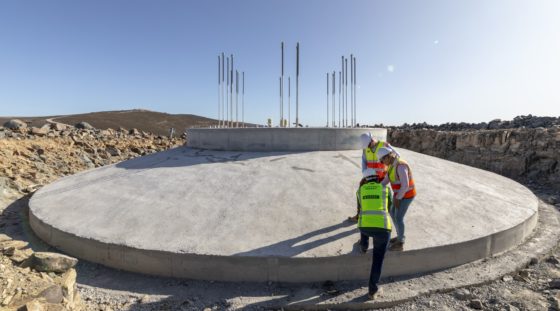
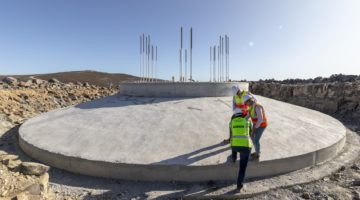
Refresh | This website www.giatecscientific.com/mass-concrete/ is currently offline. Cloudflare's Always Online™ shows a snapshot of this web page from the Internet Archive's Wayback Machine. To check for the live version, click Refresh. |
Mass concrete pours are becoming more and more present in the construction industry. As our ambition grows, the size of our concrete structures grow with it.
As society continues to grow, so does infrastructure. With this being the case, concrete pours have also seen a change. Mass concrete refers to concrete pours that involve large structures. The following information covers everything from the basics of mass concreting to the impact of temperature on concrete.
When designing a construction project, a major aspect of consideration is the concrete mix itself and there are many properties of concrete that need to be mitigated. The materials used in mixing concrete react with each other and produce heat through hydration. If this heat is not properly dealt with issues such as concrete cracking can occur. This heat rise causes larger than normal temperature differentials which can be mitigated through temperature sensors and cooling methods that ensure the quality and durability of the concrete element. This heat generation can be divided into the Pre-Induction phase where water first encounters the mixture, the Dormant Period where the concrete begins to be workable in the early stages of hydration, the Strength Gain phase where the concrete begins to harden, and finally the Steady State phase where the temperature of the concrete begins to stabilize, and hydration begins to slow as strength is gained. Careful planning and techniques are required when pouring concrete as ambient temperatures can further destabilize the concrete quality.
As the concrete cures, the core of the concrete element becomes the area where the maximum temperature occurs. The element cools from the outside in and the core may take years to fully settle. During this phase, the main issue is Delayed Ettringite Formation (DEF) where the required ettringite does not form when required and leaves the element weaker. This is a negative byproduct of when a concrete element’s temperature is too high and prevents the needed ettringite formations from occurring. The results of this will only show years later as the absence of the correct formations will cause cracks and concrete expansion, severely impacting the elements’ strength. DEF is a concern when the temperature of the element exceeds 158°F (70°C) and will cause issues with durability and service life. Ettringite is a normal process that occurs during the hydration phases of cement and aids in preventing the quick stiffening of the concrete so that it can be easily worked.
When the concrete begins to cool there is quite a large differential between the hottest point and the coolest point. There are other factors to consider as well such as the outside ambient temperature which drastically impacts the surface while the core remains unaffected.
The issue is that there needs to be the lowest possible differential to ensure enough tensile strength to withstand the thermal stresses to avoid cracking. This cracking is due to how the different temperatures affect how the concrete moves in the element, the cooler regions tend to contract while the hotter regions expand. This movement causes internal stresses and cracks, which is directly affected by the coefficient of thermal expansion as it represents the change in the size of the concrete related to the change of temperature. The lower the coefficient, the lower the volume change associated with heat rise, making the temperature differential larger. Concrete temperature differentials directly affect the strength of the element, and it is the mitigation of this difference that is the goal of workers.
There are multiple types of sensors that calculate the necessary variables for concrete curing effectiveness. As technology evolves within the construction industry so do the practices, and sensors themselves have seen many changes and upgrades as we further our understanding of concrete curing.
A device consisting of two wires made of different metals are twisted together at one end forming an electric junction. A temperature-dependent voltage is produced by the thermocouples due to their thermoelectric properties; the voltage is then measured by external equipment to estimate the concrete temperature. This sensor is very inexpensive but not entirely accurate or reliable as the wires are easily cut and installation is very time consuming.
A sensor comprised of an electric circuit board that contains a coin-sized battery with an onboard transmitter for temperature that is meant to be placed in the concrete element. A wire protrudes from the element allowing a handheld device to be connected to record and display temperature values. This device has no electrical switch permitting it to always be active, which also makes its shelf-life quite limited, they are also difficult to install, and the connectors are hard to use and can be cut or buried in wet concrete.
A sensor that is connected to the end of the wires coming out of the concrete element to store and transfer the temperature measurements over a wireless network. This sensor’s transmitter sits outside the slab because it needs to have reception in order to wirelessly transmit the data. These sensors are the beginning of the shift to a more indirect and Internet of Things based approach to concrete sensors.
A self-contained wireless concrete sensor and logger that is fully embedded in the concrete element and is attached to the rebar. The temperature measurement and logs are stored on the sensor and can be downloaded through various wireless communication methods to any device. The flexibility and ease of these sensors are the major advantages over the others as they are not prone to potential damage on the construction site following installation into the slab. The installation is relatively simple as there are no wires to be dragged outside of the mass concrete element as it is all contained within the sensor.
All types of sensors usually have the same parameters as they are rated up to 176°F (85°C), any higher would produce accurate reading. The common refresh rate or interval of temperature measurement is 15 to 30 minutes with a common lifespan of 28 to 56 days.
No matter what kind of project you are working on, you can achieve great results and ensure quality with a thermal control plan. If properly developed and executed, thermal control plans will stop concrete cracking and shrinkage, ensure adequate concrete strength gain, and prevent other quality-related issues with your concrete. To get the most accurate concrete temperature readings in the fastest possible time, use SmartRock® wireless concrete sensors. Take control of your concrete, avoid thermal cracking, achieve huge cost-savings, and move your projects along faster!
The required number of sensors per jobsite solely depends on the job itself as there is no correct answer. The shape of the concrete element is another point of contention when deciding how many sensors are needed but the actual number is up to the engineer. A factor to take into consideration is the length of the pour as the timing of the utilization of concrete can cause many different temperatures and measurement points. The combination of sensors and restraints are used to help the concrete cure effectively, the role of restraints is to help the concrete retain its shape during the curing process. The shape of the restraints has a heavy influence on the maximum and minimum temperatures of the element, thus affecting the number of necessary sensors.
Concrete cannot regulate its temperature itself and as mentioned above, the core and surface of the concrete element both have very different temperatures and behaviors. In order to counteract these effects, temperature regulation protocols must be followed to promote normal temperature readings. Methods such as cooling pipes, liquid nitrogen, and cooling of coarse aggregates are taken to manually cool the concrete element. In the past ice was sometimes added to the mixture to cool it down, but this would change the water content within the concrete thus changing its behavior. Newer methods such as using liquid nitrogen bypasses the issue of changing the water content. With this method being expensive, it also reduces the carbon footprint as less energy is used with transportation than ice and it needs no temperature regulation. A more efficient way is not to add liquid nitrogen to the mix directly but to cool down the coarse aggregates on a conveyor belt. The utilization of cooling pipes is another approach as pipes are pre-installed into the pouring area and allow for complete control over the concrete elements’ temperature. Keeping the temperature gradient minimal in a mass element is key to achieving a durable concrete structure.
Before construction begins an adequate thermal plan must be in place to ensure efficiency and quality of the concrete element. To develop a good thermal plan, one must first understand the factors affecting the jobsite such as ambient temperature, the dimensions of the project, mixture design, and others. Following this there must be a good estimate of the adiabatic temperature rise of the concrete and the placing temperatures. Following the pour all other variables must be calculated and carefully considered when deciding on cooling methods. Next is the curing process which can be strenuous without the correct sensors or materials. Should the planned steps be followed, the concrete element should have longevity and durability for any situation.