A concrete mix is a combination of five major elements in various proportions: cement, water, coarse aggregates, fine aggregates (i.e. sand), and air. Additional elements, such as pozzolanic materials and chemical admixtures, can also be incorporated into the mix to give it certain desirable properties. A ready-mix concrete design is a process of selecting ingredients for a concrete mixture and deciding on their proportions. When designing a mix, you should always consider the desired strength, durability, and workability of the concrete for the project in question.
Explore 12 Futuristic Technology Trends Solving Concrete's Biggest Challenges.
Needless to say, all ready-mix producers strive to find the perfect proportions of these ingredients in order to optimize their concrete mixes and give their concrete strength, durability, workability, and other desirable properties. It’s important to optimize concrete to ensure the lowest cost while maintaining the highest strength of your mixture. This is far from easy, as every addition or subtraction to the concrete mix entails adjustments to the components, making the process very complicated and inefficient. The solution is Giatec’s Concrete Hub app.
Concrete Mix Design
Concrete mix design is often mistakenly referred to as “cement mix design.” However, cement is simply one of the ingredients of concrete. It is a binding substance that allows concrete to set, harden, and adhere to other materials. Therefore, it cannot and should not be used interchangeably with concrete mix design.
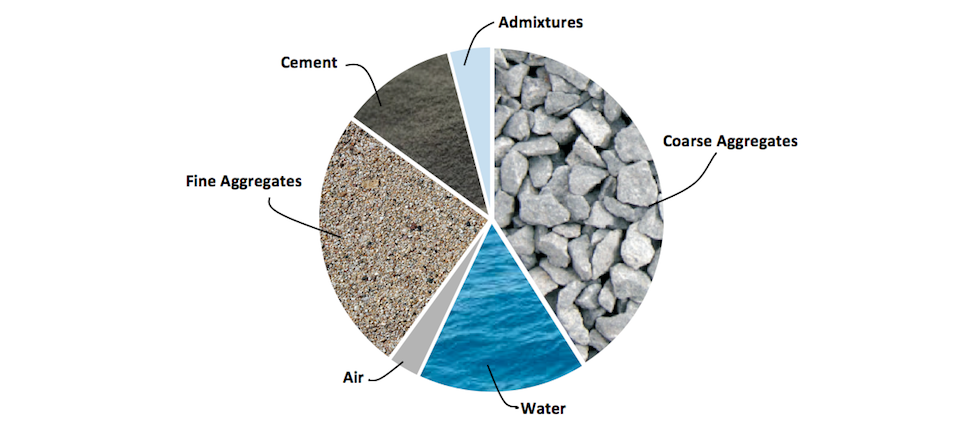
Calculating Concrete Mix
Giatec’s free Concrete Hub app now features a new mix tool that allows you to design your concrete mixture quickly and easily. No need to have the ACI standard on hand; the application provides all guidelines and performs all calculations for you.
How to Design a Ready Mix Concrete
In general, concrete mixes must follow the guidelines (ACI Committee, 2009). A ready mix concrete can be designed using the tables and calculations provided in the standard.
All concrete mixes possess unique properties, the design process can be time-consuming and challenging. The Concrete Hub app, however, solves these challenges associated with creating a unique ready mix concrete.
Concrete Hub’s Concrete Mix Design Tool
The Concrete Hub app now provides an easy, fast, and free way to perform a preliminary mix design. The app also features an add-on allowing you to create proportions for your ready mix concrete design using either the absolute volume or weight method.
The application performs all the calculations in either SI or Imperial units according to the ACI 211.1-91 standard and provides guidelines from the standard at each step via the Help icon. Once your ready mix concrete design is complete, the app generates a summary file that can be easily shared.
Learn About Concrete Maturity Sensors
Ready Mix Concrete Design Made Easy
Check our optimization solution for ready-mix producers! Learn more here!
Step 1: Slump Flow
The first step of the application requires you to define the maximum and minimum slump for the fresh mix properties.
- If the flow dimensions are unknown, you can use the Help icon to define the type of element that outputs the associated slump requirements.
- The concrete slump represents the flowability/workability of a concrete mix. For example, a higher slump allows for better placement in congested reinforced elements.
*The Help guideline is based on Table 6.3.1 (Table A1.5.3.1) of the ACI standard.
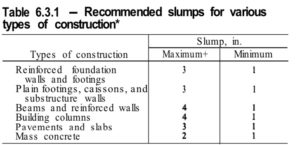
Step 2: Aggregate Size
You will also need to define the aggregate size required for the mix design.
- In general, the maximal dimension of the coarse aggregate is governed by the limitations of the structure cross-section and reinforcement design.
- Increasing the aggregate size is usually more economical as it reduces the amount of cement per unit of volume. However, it may affect the workability of the mix. In contrast, reducing the maximal size of the coarse aggregate allows your ready mix concrete to reach higher strength at an equivalent water-cement ratio.
*The Help icon available on this page proposes different aggregate sizes based on the limitation of Tables 6.3.3 (A1.5.3.3)
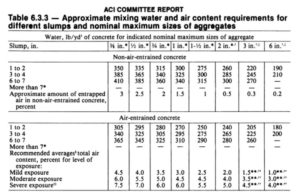
Step 3: Mixing Water and Air Content
Now you get the first estimation of the amount of water required to obtain the appropriate workability for your mix, based on the slump flow and aggregate size.
- The Concrete Hub app also suggests the amount of entrapped air required for non-air-entrained or air-entrained concrete.
- The entrapped air is an important parameter when the concrete structure is exposed to freezing or de-icing salts. In such conditions, increased air content will increase concrete durability because it allows the water to expand in the entrapped air when it freezes. This reduces the internal pressure caused by the formation of ice.
- The Help menu in this step automatically calculates the water weight and the amount of entrapped air required based on the recommended values of ACI committee Tables 6.3.3/ A1.5.3.3.
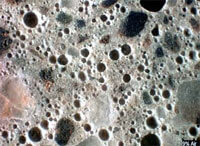
Step 4: Concrete Strength and Water/Cement Ratio
The water/cement ratio is the most important parameter of the concrete mix design; it governs the strength, durability, and workability of the concrete mix. Here, you will need to enter the required compressive strength and associated water/cement ratio.
- For example, reducing the water/cement ratio will increase the strength of the concrete and provide better durability. However, decreasing the water/cement ratio can also significantly reduce the workability of the concrete. In these cases, one possible solution is adding water reducer to the mix (see Step 7).
- Using the Help option, you can select the desired compressive strength and receive the corresponding water/cement ratio, calculated based on Table 6.3.4(a) A1.5.3.4(a)). In addition, you will receive guidelines for the maximum permissible water/cement ratio based on the structure exposition (Table 6.3.4(b)/ A1.5.3.4(b)).
- Using your input data, the app will calculate the amount of cement required. Note that the amount of cement can be reduced by introducing pozzolanic materials to the mix.
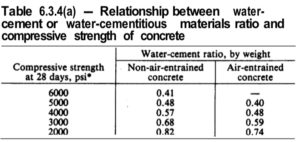
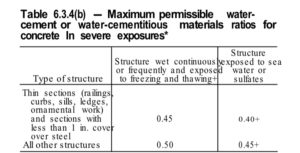
Step 4.1: Pozzolanic Materials
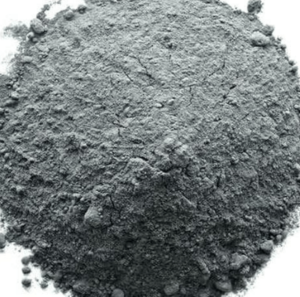
- This step also gives you the option of including pozzolanic materials such as fly ash, silica fumes, or slag in the mix.
- Using pozzolanic material to replace a portion of the cement is more ecological and economical. Typically, it slows down the curing mechanism and provides enhanced properties to the concrete.
- You can select the preferred method of calculation. Based on the specific gravity of the pozzolanic material, a new adjusted water/cementitious material ratio, amount of pozzolanic material, and adjusted cement weight will be calculated.
Step 5: Coarse Aggregate
You are now required to define the unit weight of coarse aggregate, finesse modulus, and volume of coarse aggregate per volume of concrete.
- The application will then output the quantity of coarse aggregate required.
- The Help option lets you select the coarse aggregate size and modulus of the finesse of fine aggregates. It then outputs the volume of oven-dry-rodded coarse aggregate.
- The calculation is based on values from Table 6.3.6/ A1.5.3.6. This table is based on the workability of the concrete.
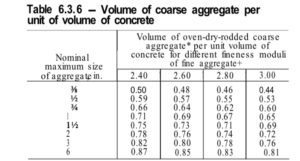
Step 6: Fine Aggregate
The amount of fine aggregate is calculated differently depending on the method of calculation (per weight or per volume) you choose.
- The volume method calculates the amount of fine aggregate based on 1 yd3 (1m3) of concrete while the weight method performs the calculation based on an estimation of concrete weight.
- Depending on the type of concrete (non-air-entrained or air-entrained), the first estimate of concrete weight can be calculated using ACI Table 6.3.7.1/ A1.5.3.7.1, which is provided in the Help section of Step 6.
You now obtained; the calculated quantity of fine aggregate required for the proposed concrete mix needed for the final calculations.
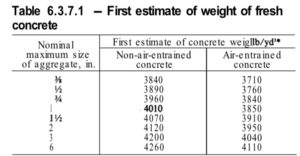
Step 7: Adjustment for Moisture in Aggregates
The last step in the calculations adjusts the amount of water in the mix design based on the input of the moisture content and degree of moisture absorption of coarse and fine aggregates.
- It is important to consider the amount of water the aggregates give to the mix and retrieve from the mix because this causes variation in the water/cement ratio.
- The Concrete Hub app computes the new quantity of water, coarse aggregate, and fine aggregates based on the input values.
- The amount of water can further be reduced with chemical admixtures like water reducer.
Step 7.1: Chemical Admixtures
This step gives you the option of incorporating water reducer, air-entrained admixtures, or other chemical admixtures to the mix composition.
- Adding a water reducer allows you to keep a constant water/cement ratio for a smaller cement ratio with compromising the strength and increasing the workability.
- Air-entrained admixtures can be very useful when trying to increase the durability and workability of a concrete mix.
Step 8: Summary Design
Finally, the last part of the process is obtaining your summary report of your findings.
- You will be asked to enter the required volume of your concrete batch.
- The app will then display the details of your concrete mix and the quantity of each material required for the specified volume of concrete.
- You can then share the summary report of the mix calculation with your team via email.
The concrete hub app provides a free, fast, and easy process to create a concrete mix design. Simple and efficient, the app performs all calculations and then prepares a summary report of your mixture
Ready to get started? Download the Concrete Hub app on:
Sources:
https://www.concrete.org/
*Editor’s Note: This post was originally published in May 2018. It has been updated for accuracy and comprehensiveness on June 2023.
8 Responses
I really like your information about concrete mix design.
Amazing post, thank you for sharing this knowledgeable post, really this is very helpful.
It’s good to know that you need to define the aggregate design before you mix your concrete. My brother wants to get some work done on his yard with exposed aggregate concrete. I’ll pass this information along to him so that he can ensure that everything is done in the right order.
I required MIX design with basic requirements with video,can you pleas share me.
Hi there, unfortunately, this is a research article written for educational purposes and and is not in our area of expertise. We appreciate your interest in Giatec and are sorry we are not able to help you in finding further information regarding concrete mix design.
I really like your information about concrete mix design. My husband and I are trying to find some concrete mix to make a patio. We’ll start looking into what goes into a concrete mix before buying one.
We need a design video please
Newly invented admixtures related to concrete