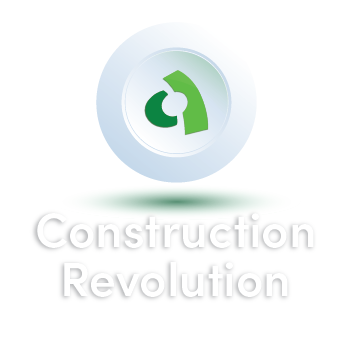
Episode 21 |
September 29, 2022
The Future of 3D Printed Construction
In This Episode
In this episode of The Construction Revolution Podcast, we sit down with Vincent Albanese of COBOD International and Ian Artur of Nidus3D. Nidus3D partnered with COBOD International and Habitat for Humanity to create Canada's first 3D printed multi-unit structure made entirely with concrete using COBOD's BOD2 construction printer. They explain how these economical and environmentally friendly 3D printed homes could become a common building style for those in need of accessible housing. Vincent describes how COBOD and their partners like Nidus3D are working together to build structures around the globe faster, with less waste, and at a lower cost. Tune in to learn how COBOD International and their partners are revolutionizing the construction industry with their autonomous building solutions.
Host
Aali Alizadeh
Chief Technical Officer and Co-Founder, Giatec Scientific Inc.
Guests
Ian Arthur
President and Founder, Nidus3D
Vincent Albanese
Manager of Strategic Partnerships, North America, COBOD
Podcast Transcript
Aali:
Hello there and welcome to the Construction Revolution podcast. My name is Aali Alizadeh and here on the show, we explore the latest trends, technologies, people, and organizations that are revolutionizing or disrupting the construction industry, and are changing what the industry will look like tomorrow. Today on the show, I’m speaking with Vincent Albanese, the manager of Strategic Partnerships for North America at COBOD.
Aali:
Ian Arthur, the president and founder of nidus3D. COBOD is the world leader in 3D construction printing solutions, with their BOD2 printer being used on projects around the world. Their vision is to bring 3D-printed and robotics constructed buildings, to every city around the world. Through partnerships with companies such as nidus3D, they’re making this vision a reality. Nidus3D is using BOD2 printer on projects throughout Canada, including the first of its kind residential 3D-printed project in the country.
Aali:
Today, we’re going to cover a very interesting topic and that’s concrete 3D printing. We have two industry leaders who are trying to push the boundaries of science and technology to make the 3D printing happen in the concrete industry, in the construction market. Before we begin, let’s just start with the introduction. Perhaps we can start with you, Ian.
Ian:
Thanks, and thanks for having me on the show. It’s a pleasure to be here. My name is Ian Arthur, and I’m the president and founder of nidus3D.
Aali:
Welcome to the show.
Vincent:
Yeah. Thanks for having us on there. Very, very exciting to see what you guys got going on for the industry. My name is Vincent Albanese. Been with COBOD for about a year now.
Vincent:
I always make the joke, I was the first American for the company. Yeah. I deal a lot with all the partners and customers, from customers to universities, to even helping set up our US office in South Florida.
Aali:
Great to have you both on the show. Before we get to the actual question, so one big question for the people who are not familiar with the 3D printing.
Aali:
Is that what is concrete 3D printing and how does it work in the construction industry? Ian, maybe you can in layman’s person terms, explain how does it work for our audience?
Ian:
We get asked this question all the time, and the first thing we do is point people to 3D printers that they might be more familiar with. The little ones that some folks have in their garage or workshops, or that you’ve definitely seen in universities. Then we ask them to imagine that 1,000 times bigger.
Ian:
The COBOD system is a huge gantry system with an extrusion nozzle, but what we’re extruding is concrete instead of a polymer or a metal filament that would come out of a smaller one. The method is very, very similar. You’re layering concrete one layer at a time in an automated fashion. Slowly, layer-by-layer, you’ll see a building come up from the ground.
Aali:
That’s very interesting. Vincent, what is your description of concrete 3D printing?
Vincent:
Yeah. Ian nailed it for the most part. If you look at the small 3D printing, that’s where you get your scale. But if you actually look at the process, the way I explain to people, it’s like laying icing on a cake. That’s basically what the printer is doing. It’s laying layer-by-layer on top of each other. Eventually, you’re going to be able to get your monolithic look on the side.
Vincent:
Yeah. Basically, what we did is we took that small 3D printing and we blew it up. For the most part, I sell it sometimes talking to people and explaining to them. I say, “I 3D print houses,” they still think small, plastic houses. But then I show them pictures and they’re amazed. To be honest, sometimes it breaks their brain, but then you have to dive into really what the process looks like.
Ian:
Honestly, that’s almost universal feedback when people finally see in person. We’ve done so many presentations of the technology. There is a remarkable difference to showing it to someone on a TV screen or something like that.
Ian:
Then having them arrive onsite and watch them crank their neck all the way up to the sky and go, “This thing is huge.”
Aali:
That’s great. I understand that the 3D printing in the concrete industry has come a long way from equipment, tools, materials.
Aali:
Specifically on the materials, what are the advancements that have been made, to make sure that these layers are poured as easily as possible and are set as quickly as possible, so that it’s ready for the next layer to be laid?
Vincent:
Yeah. This is a big topic around the industry, because for most people when they think about 3D construction printing, they just see the printer. They think that’s it. You just click a button and it starts building a house for you. People forget the material side, which is, to be honest, a little bit more important than the gantry system theirself. The technology with the gantry system is nothing new. It’s been around since the ’80s, but what we’re doing with concrete is completely different.
Vincent:
To set a precedence, there’s two types of materials used in the industry. There’s mortar and there’s concrete. You ask people what’s the differences, they’ll say basically the aggregate size. Concrete uses a little bit more aggregate size. But for 3D construction, they’re actually completely different. When you look at a mortar, a mortar mix will be a mix made, let’s just say, in a factory. It’s going to have admixtures and additives built into the product already.
Vincent:
All you’re going to do is you’re going to take the mortar mixer, your cement powder, put it in the silo, and you can mix water to it. That’s where the industry started because it was super easy to go that route. But when you look at the overall cost of dry mix mortar, you’re picturing 450 all the way up to $800 a cubic yard.
Ian:
And more.
Vincent:
We’re trying to build cheaper here and more, yeah. So we’re trying to build cheaper here. What COBOD discovered about two and a half years ago was, “Hey, we can actually make real concrete.” That involved two parts. That involved one, making a batch plant that can mix the concrete for mobility and on-size demand, and that was creating the D.fab solution with CEMEX.
Vincent:
The D.fab solution with CEMEX, is really what makes a concrete 3D printable. It has accelerants, plasticizers, super plasticizers, so the concrete can make its form and then cure quick enough. So when the printer comes around for the next layer, you don’t have to worry about the following layer.
Ian:
Getting the timing between those two layers is so important. We do all sorts of calculations on that when we go out. So nidus exclusively uses the concrete printers for a lot of reasons, and I’ll get into a few of them. You need to find this perfect point in time, where you’ve measured your layer time and it’s soft enough that you have consolidation between layers, that you have the one layer adhering to the one below it.
Ian:
But strong enough that you’re not having compaction and having the wall slide down or collapse underneath the weight of the new layer. Nailing that exact mixture and how much admixture needs to be in the mix at any given time, it’s challenging but it’s definitely manageable. We found our key operators have just significantly increased their ability to recognize what needs to be done at any given point in time.
Aali:
Very interesting to optimize that time of pouring, so to speak. From a materials’ perspective, I think Vincent, you mentioned some specialty mixes. But from a practical perspective, Ian, do you think that these materials are readily available?
Aali:
One of the advantages of regular concrete, is that aggregate, sand, cement, water’s readily available everywhere in the world, and that’s why concrete is so popular. But when it comes to 3D printing concrete, you have, as you mentioned, there are specialty mixes. From availability perspective, how does it work? Can you do 3D printing everywhere in the world?
Ian:
We can because we print in concrete. We made the conscious decision not to use the mortar mixes from a cost perspective and an availability perspective. Canada is a massive country with a population that is spread out over a huge area. We have ambition to go into remote communities with this technology and deploy housing in communities that are very difficult to build in traditionally.
Ian:
One of the key factors for us to be able to do that, is being able to source those materials locally. We’re based outside of Toronto, but we want to move into the west coast, BC, Vancouver in the near future. If we had a source of mortar in Ontario, the logistics of making sure we could access that in BC are almost insurmountable. Whereas high quality sand, spec, aggregate, Portland cement, and then the admixtures that come from COBOD are all readily available.
Vincent:
That’s what we wanted to do. We wanted to make sure that the material, not just the gantry system itself, was on demand, but the material system was on demand itself, because our batch plant, that’s what you’re going to do. You’re going to source your raw material. Your sand, your aggregate, your cement, your water and you’re going to batch it onsite. The admixture we use from CEMEX is only 1% of the actual material, so 99% of it is raw material.
Vincent:
The nice thing with CEMEX, CEMEX is a global company so we can get their additives all over the world. But by doing this with concrete, we’ve been able to achieve whatever your average price of concrete is. I know for at least the US, it’s around $100 to $115 a cubic yard. Well, now we’re able to meet those prices because we can batch the concrete onsite. Then we also don’t have to worry about people bringing it onsite, logistics cost, things like that.
Ian:
The technology, when you have that price equivalency in the materials that are going into this, we actually have a price advantage over other companies that are using mixed concrete, because we only mix the exact amount that we need. We are operating with 3% to 5% waste, and most of that’s what’s left in the hose at the end of the night that we have to pump out. We’re only mixing exactly what we need. You can’t really order a third of a truck of concrete to be delivered to site.
Ian:
Everyone over orders concrete and then they just dump whatever’s left. They have alternative uses for it, usually back making traffic pylons or whatever it is that they need to do. Not the pylons but the dividers with the leftover concrete at the end of every day. But that’s almost paid for twice. When you spec out a concrete order for a job, everyone traditionally over orders. We mix exactly the amount we need for every job and no more.
Aali:
That’s very interesting. On the same topic, the quality of construction is obviously key in getting structural, I think, performance met. At the end of the day, get occupancy permit for that particular structure. The quality and performance evaluation has been well established for regular ready-mix concrete. The type of test that you would do, a slump test, air test, strengths test at different ages.
Aali:
How does the quality in general work or quality assessment work for the 3D printing concrete? What are the test methods that have been developed or standardized to ensure that the quality of the final product meets the performance criteria that is set for that particular 3D-printed structure? Ian, maybe you would like to start. Since you’ve been working with GCs, obviously they have very strict rules on their performance criteria.
Ian:
Yeah. Another, I think, advantage of the concrete approach to 3D printing, is that we developed a mix profile that is in Canada. The authority is CSA, that’s a CSA approved mix. The mix that we are printing is no different than the mix that is being used all over the place in concrete based construction. We’re not doing anything particularly different. What we’re doing is placing that material in a different way. We really do emphasize that from a code perspective, that this is masonry construction.
Ian:
We have been building masonry buildings for thousands of years. I actually just pulled out my phone to have a look, because we just got results back from our 28-day tests on the material that we deployed on our last job. We take a sample every day, we turn on the printer for compression testing. We do the slump testing of the mix ahead of time, and know where it needs to be for printing and everything. We hit 48.68 MPA on the first day. We sped up the printing process on the second day. The MPA did drop, but it only dropped to 42.31.
Vincent:
Still, very high, 40. That’s around 5,000 PSI to all the American listeners. That’s around 5,000 PSI to all the Americans listening.
Ian:
There you go. Yeah. Sorry, need the translation. Thanks, Vinnie. That’s really high. The building standard is 32, so we’re exceeding it significantly. We think we can improve on it even more, as we figure out. One of the amazing things about 3D construction printing, is it’s taking data and applying it to a sector that really has not been data driven, in a really significant way in a long time.
Ian:
We’re collecting data on every layer that we print. We can measure what the temperature was when that layer was placed. If we run into failures, if we run into things, we can go back and drill down, and find out exactly what variable was different from one layer to the next. Identify those and be able to standardize and correct those over the long-term very, very easily.
Aali:
Very interesting. Vincent, from a robotics perspective, what are types of maybe sensors that you would use to monitor the whole operation?
Vincent:
Yeah. To preference, my background was in mechatronics engineering. I was in university right when the Industry 4.0, IoT, right when that was kicking off. I’ve spent some time in advanced manufacturing, Amazon plants for it, you name it. I’ve seen what technology is out there. Ian made a good point that construction is so old, it’s very hard to study, why? Because there’s no data behind it. There’s things that you can do from the entire life cycle. One, you could put sensors on the printer to understand how you’re printing, visual sensors, AI.
Vincent:
That kind of stuff to understand the print and the quality control while you’re going with it, and creating the algorithms behind there. Then you can take the sensors to the batch plant as well. How do we automate that process as well by adding humidity sensors, temperature sensors? So as concrete, as the day changes, as the heat and the environment changes, your concrete mix is going to change as well. How do we automate that process? Then we’re looking at some of the other cool stuff like VR and AR.
Vincent:
I have a setup right now, where I’m able to put my virtual reality goggles on, see the full size of a printer. Right now, we’re just using that for demo purposes, but we want to use that for training. Then we also want to use that for remote operations. I know they use remote operations for large manufacturing plants already. There’s no reason why Ian can’t be in Ontario and doing a project, let’s just say, in Toronto or Windsor, Canada.
Vincent:
And not being able to see the full aspect of how his machine is operating on any given day. One key is we work with very large, industrial automation brands as well. People like the Rockwells and the Siemens of the world, they have that technology already created. It’s just a matter of, “Hey, how do we convert it to the construction aspect?”
Aali:
Awesome. That’s amazing. Vincent, maybe on the same line, you mentioned about the key elements in your technology and how you’re automating the whole process. I understand that BOD2 printers, were bestselling 3D printer of concrete. What makes it so popular?
Vincent:
Yeah. I was thinking about this answer and we’ll take a little different approach, but for the most part what has made us so successful is our partners. People like Ian at nidus, from our investors at GE, Perry and CEMEX. Without our customers actually taking the challenge with us, and exploring different applications and different theories with that, we couldn’t evolve it. Which leads me to that second point, is we are one of very few, if not one of the only 3D construction companies that are doing real projects in the while.
Vincent:
We’ve done it on all six continents. From schools in Africa, to three-story apartments in Germany, to Canada and North America, all the way to South America and Australia as well. We really have a global presence and basically, we’re able to take feedback very well and adapt the technology. For the most part, a lot of people are going to all start on the same level field and come across the same challenges. The nice thing is we have so many customers that we get constant feedback that we’re able to adapt not just the machine, but the material and everything else that goes with it.
Vincent:
Thirdly, it’s the people that drive the company. Ian could tell you, it’s some of the smartest people in the world I’ve ever worked with, but it’s a lot of young, driven professionals that really want to make a difference in this world. And really want to create an impact and some change in one of the most outdated, oldest industries in the entire world.
Aali:
That’s amazing. You also have a product called COBOD Mini Batch Plant. How does this product work with the BOD2 printer?
Vincent:
Yeah. That was the batch plant we were talking about that enables us to make concrete, so that’s the first in its kind. Actually, mini batching is actually pretty uncommon in the concrete world, because you’re usually doing tons and tons of concrete pours.
Vincent:
We work with a vendor that has been able to create this batch plant specifically for mini batching, but more specifically for 3D construction.
Aali:
Ian, from your perspective, you’ve probably worked with other 3D printers or you’re familiar with the other technologies in the market.
Aali:
What makes COBOD so special that you have selected them to be their exclusive partner and use their technology for 3D printing?
Ian:
I think I would echo some of what Vincent said, in that it was real world examples of this technology being used by third parties successfully. You can look out at other companies that will be entering the market and have their printers out there, and they’re just not there yet. Our estimation was that COBOD was three to five years ahead of anyone else in this space. Having visited them in Denmark, we think that’s going to continue.
Ian:
Because they have their second generation printer in market, being deployed on a large scale. And are working on the next round of improvements, while everyone else is still trying to get those printers deployed in the first place into the field. They have a huge leg up, I think, on the competition. I think the support from the company is fantastic and was fantastic from the very beginning. From the first point in time we reached out to COBOD, they have been supportive. They have a 24/7 support line that you can access globally, which is fantastic.
Ian:
Then the whole idea, which Vincent also touched on, of all these different groups that are running into similar problems or different challenges. There’s a lot of communication between people with COBOD printers. We end up on calls with folks from Australia, or down in the States or England, and Great Britain talking about, “Oh, we ran into that too. Oh, what was your solution? This was our solution.” We are at the very forefront of a brand-new industry.
Ian:
When you talked about testing standards and stuff like that, I laughed because it’s really internal right now because a lot of those international standards are currently being developed. It’s actually these companies deploying this technology in the field and taking those tests, and working with universities and governments, that are going to create all of that. The nomenclature, how we actually refer to the different parts of 3D printing. We get to be a part of that at the very front end.
Ian:
Working with COBOD to do that, we’re going to define an entire sector as a group using those printers and with COBOD as a manufacturer.
Aali:
Actually, continuing that topic in a way, I would love to hear more about the project, the residential project that you completed in Canada. As you mentioned, there’s still a lot of standards being developed or guidelines developed for 3D printing of concrete structures. And yet, you were able to work collaboratively together and with the general contractor to complete this multi-residential structure, and get occupancy permit at the end of the day.
Aali:
We all know, construction industry is not that open to adopting new technologies because of all the liabilities that are associated if something goes wrong. I would love to hear how that project was started. How did the GC said, “Okay. I’m going to try 3D printing technology,” and you work together to make it happen?
Ian:
I think that’s a really, really good question. I think at the very beginning of it, was that the general contractor or the project leader in this case, was Habitat for Humanity. They have been working with COBOD printers on multiple continents in multiple countries for quite a while. That partnership, having an organization like Habitat for Humanity wanting to embrace a new technology honestly, goes a long way.
Ian:
Because then it’s not just nidus3D approaching building inspectors with building designs. We’ve got the weight of a globally recognized, affordable housing institution that can lend their pull to getting these projects to go ahead. Now, that’s not to say that we cut any corners or anything like that, but it’s just getting in the room and getting them to listen. Really what it is, it’s a collaborative process. It’s, “Okay, we want to put up this structure. What are the things that we need to incorporate to get to the place where we do get residency permits?”
Ian:
The Leamington project, which is the one you’re referring to, was also a partnership with the University of Windsor, which has one of the best concrete labs in Canada. They had been doing testing on 3D printing for a year before we actually started deploying this concrete onsite. They had a lot of data that they were relying on, which helped us do it. I think a willing partner in the municipality. So the building inspectors or the chief building officer wanted to work to get this thing done and figure out what we had to put in place to do it.
Ian:
Our approach from the very beginning for these proof of concept and early projects, has been to not actually rely on printed material to be structural. Technically, if you really looked at these projects, I think they would count as the windbreak. We add additional traditionally poured columns to support roof structures and floors, and we engineer those columns to be able to take the entirety of the weight of those multiple stories, and we’re printing around them. It’s an extra added feature.
Ian:
It adds a little bit of cost but not a significant amount of cost to the project. It has allowed us to work with engineers and building officials, to make sure that we do get to a place where these can be permitted.
Aali:
Are there people living in and staying in that building today?
Ian:
Not quite. We’re getting there. The biggest delay on that one so far, has actually been the type of low expansion foam that they’re insulating with was suddenly unavailable, as the story is in so many places, sectors right now. There’s a bit of a delay on that. But by early fall, yes, there will be people living in that building.
Aali:
Amazing. That’s amazing.
Ian:
We’ll also have our second project will be completed by early September as well and fully finished, so we’ll be able to provide updates on that too.
Aali:
That’s amazing. Vincent, you work with other projects, other contractors. In general, you need to get the buy-in from the contractor and also the Structural Engineer of Record.
Aali:
What are the common questions or hesitancies that are brought up by the structural engineers, in particular?
Vincent:
Yeah. For the most part, it just takes some educating because I’ve spoken with quite a bit of structural engineers. And once they look at our drawings and look at some of the things we do, they realize they’re not doing anything new. Concrete structures are built all over the world. This is more or less just a different form of pouring the concrete. Sometimes when you lead the conversation, is we’re 3D printing concrete.
Vincent:
Like I said, it could break the brains. But if you more just take it down to a base level, “Hey, we’re using a tool to pour concrete to build concrete houses. This is how concrete’s going to perform. This is how the thermal insulation is going to perform. This is how you do windows, this is how you do load-bearing walls.” Once you just do a little educating, it immediately clicks. But then again, there is a lot of liability behind it.
Vincent:
For the most part, my experience with customers is you need a structural engineer to get onboard with you. Then the city, it’ll be easier to get through the city processing and the building code, stuff like that but it all starts at the technical level. The more data we can have to back them up, and the more use cases we can show them, the easier it is, not only for us to educate the engineers, but the industry as a whole.
Aali:
What are some of the most interesting projects that you’ve worked on around the world?
Vincent:
Yeah. I wish I could speak some of what we’re working on right now. Unfortunately, you got to keep a little quiet. To be honest, what we’re doing with GE is pretty fascinating. The reason why it’s fascinating too, because not only is it a new project, but we also had to create a new printer for that. That printer that we built for GE, it’s going to be 65 foot by 65 foot, so absolutely amazing structure. A feat of engineering to say, but it’s also the first dual access construction robot out there.
Vincent:
Not only did it have a head for 3D printing, it has an automatic crane to insert rebar into the pedestals. As the concrete tower’s being printed, the printer head will move to the side. The crane will pick up the rebar and insert it itself. No manual operations required for that. That’s a really cool project to show that, “Hey, most people we’ll say are going after the residential market. But the commercial and industrial sector is also something you can explore as well.”
Aali:
Very interesting. What is the, I guess, maximum number of stories that you can build, say two, three, four, using the 3D printing technology?
Vincent:
Yeah. Right now, the farthest we’ve had tested was three floors with the BOD XL that I just mentioned, was 65 foot by 65 foot. In theory, you can go up to six to seven stories, but we haven’t had, let’s just say, a showcase example yet.
Ian:
We’ve been testing and pioneering what we call print in place lift in components, where we actually print the veneers. We design them in a way where they’re meant to fit together, and then we lift and place them with a crane, which has actually allowed us to do structures that are bigger than our printable area. We haven’t used that to increase height yet, but we have a potential commercial customer right now, looking at some warehouses that are well above the printable height of the printers that we’re going to have.
Ian:
We’re going to be testing over the winter if we can actually hit it. They want 40 feet of ceiling height on these warehouses. We’re going to be testing over the winter, if we can print components and then provide the structural connections needed to be able to go that high with printed materials. Very, very exciting to be part of that.
Aali:
That’s amazing. Apart from structures in a commercial, residential, multi-story structures, do you see 3D printing technology used, for example, in the construction of bridges perhaps or other types of structures?
Ian:
Absolutely. We’ve had a couple different groups approach us. I think the only thing holding us back from executing it, is the data and testing data behind that. We can totally move into it. Anything I think that you would call either feature rich or unique, one-off, one-off pieces, the printer is uniquely good at executing those projects. Traditionally, you need a minimum unit yield to make a traditional form and fill it up for cisterns or whatever it is.
Ian:
If you have unique requirements and you only need one of them making the 3D model, and then 3D printing it is far more feasible than building a form. We were approached by a group that runs train stations. For safety, they need these secondary egress bridges or tunnels that go on and off tracks. But every single platform had different specifications, so no two bridges were going to be the same. The cost per bridge with a traditional construction method, would’ve been prohibitive.
Ian:
What we’re exploring is even if we could just use our printed material as the form that they’re pouring into, we can print those forms very quickly and efficiently, and at a low cost. Then we can put the reinforcement in and pour traditional bridge, and it performs based on the poured material, not on our forms. That would be a way for us to move into that sooner, before we have those years of testing that are really required to get a new technology approved for infrastructure.
Vincent:
This is the nice thing about being active on six continents is we have people like Ian and other customers to explore different applications. We strictly know where we can fit in the situation. We are by far the most knowledgeable when it comes to 3D construction, but we need our customers to go out there and to test the applications to make partnerships.
Vincent:
One thing we keep talking about is standards, and is why one reason I work with a lot of universities. Because when we explore new applications, especially for things like construction, because of the liability behind it, we need the testing. Universities have the resources that they could come in and they can do the research that help us create these new applications.
Aali:
That’s amazing. I think Ian referred to maybe tunnel construction. We know today there’s a method called shotcrete in that particular application. I’ve seen robotic arms that are used to basically apply shotcrete.
Aali:
Would you consider that a 3D printing method or by definition, it’s not falling under 3D printing? I don’t know. Vincent, you might be able to…
Vincent:
Yeah. What I would like to say, one thing COBOD is doing, we’re branding not only as 3D construction, but we’re also taking a different route right now where we’re going to explore construction robotics. How do we use a robotic arm to do stuff like that? That’s, let’s say, a whole part of the whole construction robotics process.
Vincent:
3D printing, let’s just say, by definition it’s additive, it’s layer-by-layer. But like I said, that would be more of, “Hey, what are different applications like windows, doors, painting, drilling, insert rebar by itself?” That’s more of, let’s just say, a construction robotic applications approach.
Aali:
Maybe changing the subject a little bit, you both have very interesting backgrounds that are not in the construction industry.
Aali:
Curious to know what brought you to this industry and what’s fascinating you to continue your path and journey in the construction industry? Ian, perhaps you can start first.
Ian:
Yeah, sure. Just for the listeners out there, I think what you’re referring to is, previous to founding nidus, I was actually a politician at what would be a state level in the US, but they’re usually full-time jobs up here so making that transition. I was fascinated from a policy perspective and there’s a global housing crisis. We have a housing crisis in Canada. I know there’s a housing crisis throughout the US and in Europe as well.
Ian:
Really looking at what the policy recommendations were, and realizing that none of them were going to adequately address the supply challenge we have on houses. That we had to fundamentally change how we are building, if we were going to step up to these challenges. Layer climate change on top of that and the need to build climate resilient buildings, adverse weather events are becoming more and more frequent. The stick frame, wood buildings that are the standard, are not going to be adequate that far into the future.
Ian:
We need to do things differently if we’re going to prepare from a climate resiliency perspective. I think I was looking at that and looking for technologies that I thought could meaningfully move the needle on the housing supply, be it affordable or otherwise, any of it. We need tons of new commercial spaces if we’re going to keep the economies in any of these countries growing. The demand was there, the need was there. I felt that construction as a sector, had the potential for significant disruption.
Ian:
Materials have changed so much in the last 100 years. We are working with materials that no one could have dreamed of 100 years ago. Spray foam insulation, gypsum board was a revolutionary when it came out. Whatever it is that you want to look at, triple-pane windows, higher efficiencies. The materials have changed, the processes have not. ICF are bigger bricks, they still have to be stacked, they still have to be tied together by labor.
Ian:
What 3D construction printing does, is it’s the first technology I have seen that begins to fundamentally address the process problem. That the huge amount of the cost in building and in ability to provide affordable housing, has to do with the processes. I think 3D construction printing is the beginning of a process transformation that could help solve those issues that I was talking about.
Aali:
Thanks, Ian, for sharing your take on the industry, and also how your background made you come to this industry and create a positive change for our future. Vincent, we would love to hear about your background, how you came to the construction market.
Vincent:
Yeah. You can say construction’s a little in my blood. I come from a long line of bricklayers. My father, my grandfather, his father before him, so it was in my blood. Actually, when I went to Purdue, I did my undergrad at Purdue University. I actually started in construction management. I was a sophomore at the time and I got to intern with AECOM, which is the largest, if not one of the largest construction companies in the entire world.
Vincent:
To be honest, I remember going in day after day, not one, enjoying what I was doing, but two, looking at the people I was working with that have been in construction for a long time. It was, “Hey, I have to get up for another day and go to work. Who wants to do that, especially if you’re a college kid paying all this money to get a college degree?” I didn’t want to live that lifestyle. At that time, I took really just a reflection and I was able to change into mechatronics engineering, which honestly, I didn’t know what I was getting myself into at the time.
Vincent:
But little did I know, Purdue University is one of the largest in the world when it comes to industrial automation. They actually helped create the cybersecurity layer for Industry 4.0. I got to go work for companies like Rockwell Automation, Siemens, ABB, after college and during my internships. I love manufacturing and I love where the technology was going. To be honest, one day I saw a YouTube video of a 3D printing construction robot.
Vincent:
For me, it immediately clicked because I knew my background and I knew where the industry was headed. That the technology is viable enough to, “Hey, this can actually do what it wants to do.” I did research for six months, really tried to dig into it. And next thing you know, I was on my way to Copenhagen, Denmark. Got to go work for COBOD and it’s been a blast ever since. I get a lot of freedom to do what I do. Really, if you’re going to dream, dream big. The construction industry is the largest in the entire world. If you’re going to make an impact, why not start there?
Vincent:
From the projects we’re doing in Africa, to schools, to really the impact it can have on an environmental and sustainability aspect too. It’s really where passion and purpose came together for me.
Ian:
Yeah. I think that’s so important that we are innovating on a daily basis. Hugh, the other owner of nidus3D and myself, we show up in the office at absurd hours in the morning and we’re excited to be there.
Ian:
The days are crazy long, but we are defining a sector right now and that’s such a unique opportunity. You don’t get many chances like that in your life. I think it’s just incredible to be part of this.
Vincent:
I remember my first week in Copenhagen when I met Ian. He looked at me and he goes, “Man, you’re lucky. You just got on board the next Tesla.”
Aali:
That’s great. Thanks for sharing the journey. Both of you, I think Ian especially, you touched on a point about environmental aspects.
Aali:
Can you maybe elaborate a little bit more on how 3D printing in the concrete industry can help with the environmental aspects, whether it’s material use or global, greenhouse gas emissions?
Ian:
For sure. I think you have to start with acknowledgement of the carbon problem that concrete actually has. It’s a huge emitter. I think globally, the concrete industry would be the seventh largest emitter in the world or something like that. It is significant in terms of the emissions it puts out there. I think fundamentally, we do have to examine the material that we’re using and come up with new and innovative ways of lowering those emissions. I think that the tool of the printer, the BOD2, helps from some aspects of that. One is the lack of waste.
Ian:
We are using and mixing only the exact amount of Portland cement we need. Portland is really the thing that causes most of the emissions that you’re referring to, so I think that’s important. I think by mixing onsite, we are doing larger deliveries and keeping more trucks off the road. There’s an inherent environmental efficiency there, where we’re burning less fuel to get product onto site. Because we do a big delivery of sand, aggregate, we maybe have one or two trucks that arrive at a site to finish an entire building, which is pretty unique.
Ian:
I think those things, the nature of the efficient use of this technology, is a key aspect to why this has the potential to be more environmentally friendly. I think we have to, and there’s a lot of smart people working on this, begin to look at how we actually lower the carbon footprint in the process of making Portland. I know that there’s some huge companies working on this. There’s a Bill Gates back startup that is working on a solar-powered cement factory.
Ian:
So rather than needing to hit those temperatures solely with the burning of natural gas or whatever they are burning, they can do part of it with solar. Stuff like that I think is key. I think introducing recycled materials into it. There’s recent results of a study from a US university, that looked at recycled glass aggregates, which had looked like they had really promising potential to be incorporated. I think that’s really important. That’s on the material side.
Ian:
I’m talking a bit long here, but I want to touch on the performance side of it because I think that’s the other part of this equation. We are building what we like to call multi-generational, 100-year homes. With very little, additional cost, you can increase the cavity depth between those two veneers to whatever you need it to be, to hit the environmental performance you’re looking for. If you want to hit LEED Platinum or Passive House standards for insulation, we just make that cavity bigger.
Ian:
We introduce more insulation into that cavity and we can create buildings that are climate resilient because they’re structurally strong, they’re made out of concrete, that are going to last significantly longer than any wood frame house. If you look at the cost of replacement and the carbon associated with replacing homes more frequently, it’s significant. We can get them to a place where you could heat them or cool them with very, very little energy.
Ian:
In Canada, we call it heat it with a candle, is the dream that Canadians have because the costs are so high up here when it gets real cold in the winter. I think there’s a lot of opportunity to get to a place where these have the potential to be hopefully carbon neutral, and maybe even get to a place where they’re carbon negative. But it’s definitely one of the tasks we have ahead of us to figure out how to do that.
Aali:
I think what you also refer to is you have a much tighter control over and consistency over the production, compared to the traditional, ready-mix industry where if there’s a lot of variability in the quality, even for the same concrete pour. That means that with a consistent production, you can optimize the amount of cement and material use. You mentioned about less waste at the end of the day, that are going to contribute to the environmental aspects of construction.
Aali:
At the end, I would love to hear your views on the future of concrete 3D printing industry. As you mentioned, we’ve come a long way, but there’s still a lot of things to do to make sure that we get the larger adoption and wider application of 3D-printed concrete instructors. What are your views on the future of 3D printing and what’s going to happen in the short-term and long-term from your perspective? Vincent, maybe you can start first.
Vincent:
Yeah. There’s probably three things. The first one is just applications. Right now, there has yet to be an application we explored where we say, “Hey, we can’t do this.” The more applications we get from COBOD, the more we can explore. Really, the limitation is truly endless. Whatever your imagination can create, at least let’s explore the opportunity because it might not be viable now. Well, that’s just because traditional methods don’t make it viable.
Vincent:
How do we rethink and how do we have the industry and our customers rethink about design? Then the second one, it’s going to be material. Like I said, creating more sustainable, environmental material. What goes along with that is my third, is university and research. The more research, the more testing and the more data we could provide to the industry, the more, let’s just say, flexibility we’re going to be able to have to explore new materials, new applications, new partnerships.
Vincent:
Additive manufacturing is, let’s just say, well known in general, let alone 3D construction. The biggest thing that we can do right now, is educate as much as possible. The more we can get out there, the more we can have people approach us and look at partnerships, and look at collaborations and different opportunities. As I just said, really we’re very optimistic about anything. We have engineers to help us with structurals.
Vincent:
If we have to redesign the printer, if we have to create a new printer to meet specific applications, we’ll go that route. It’s really, like I said, if people come to us and say, “Hey, I want to do that,” we’re always open for the challenge.
Ian:
Yeah, same question. I think fundamentally, it’s the beginning of what I talked about earlier, which is a process change to how we build. I would echo Vincent’s sentiments in that there is near unlimited possibilities with where you can take this technology. I think near-term, the job is to get it deployed in as many different contexts as possible. That really is linked to that education piece where we have to go out in the world and show people that this can be done.
Ian:
I think that we are at a point in time, where there is a remarkably receptive sector for this technology, and a need from a political standpoint to find solutions to address the crises that we’re facing. I think we’re at the right point in history to introduce this process change. I think that’s really important. We expected, for instance, a lot more pushback from traditional builders, but there’s such a shortfall of laborers that they say, “Wait, you can do this with less people? Oh, okay, I’m interested.” That’s only going to get worse.
Ian:
The baby boomer generation is retiring and exiting the trades, and we do not have replacement bodies for them, nowhere near it. That labor shortage over the next several years is only going to get worse. We have to have solutions for it. Again, I think that’s sort of a near-term. Long-term, the efficiencies that this technology provides creates an opportunity to add on other efficiencies. You have this wonderful technology that places material layer-by-layer. Vincent was talking about the automated placement of rebar reinforcement.
Ian:
What we think is really important is understanding that between every single layer, you have a free point of interaction. A point of interaction you don’t have to drill, you don’t have to core. You can place stuff between layers, that can then interact with the other parts of the building for almost no additional cost of building. Suddenly, you’re in this place of saying, “Okay, we’re replacing this in a really cool way. What are the other systems that need to go into a home, and how do they suddenly change how they interact because it’s a 3D-printed structure?”
Ian:
I think that pushing the boundaries on what the printer can do and what Vincent talked about is really important. Then finding those other businesses or groups out there that want to take on other parts of the building envelope, and figure out how they improve that section of it. Bring all that together to a place where we can put up housing at a price that people can afford it, and in a timeframe that isn’t three and five years long sometimes.
Vincent:
Really, just to add on that, the biggest hurdle that we’re going to see right now is there’s no life cycle for 3D construction. That means there’s no one being educated on it. People go to get a mechanical engineer degree to build cars. There’s no one setting that foundation. We’re working on that foundation right now, but it’s going to take a year or so to really get the course to the classrooms.
Vincent:
That’s going to be the biggest thing, is making sure that we have the next generation coming into the construction field. I hope people listen to my story of hey, how I entered it was old, boring and I didn’t like it to now, like Ian said, I wake up every day and I love what I do. It’s super exciting. We really get to go explore all the way from here to really all the way to the moon, as we say.
Aali:
Speaking of that, I think NASA did a competition on building 3D-printed homes or structures on Mars. When do you think we’ll see the first structure outside earth?
Vincent:
As our CEO Hendrick says, “Let’s master building on earth first, and then we’ll take it to space.”
Ian:
No. I think that one of the most important things in this sector right now, we were really, really careful on press and media until we had something out of the ground. That is not a common approach in 3D printing right now. There’s a new group every day that says they’re going to do something that no one else has done, and they’re going to be the ones who transform it.
Ian:
Then when you look at what’s actually deployed, I think COBOD’s probably responsible for most of the actual structures in the world. I think the approach of doing first and then claiming later is really important. One of the things that attracted me to COBOD and one of the things we try to do at nidus, is make sure that we are delivering on what we say we can do. When we call you up and tell you that we’re going to build on the moon, we’re absolutely going to be building on the moon.
Aali:
Thank you so much, Ian and Vincent, and I hope your partnership takes you to the moon one day soon. Thanks again for your time, and sharing your experience and expertise with our audience. This was a very, very interesting talk.
Aali:
I really enjoyed talking with both of you, and listening and hearing your feedback on the 3D-printed concrete structures, and how this industry’s evolving in the short-term and long-term. Thank you so much for your time and being with us today.
Ian:
Thank you.
Vincent:
Thank you for having us.
Other Related Episodes
Episode 56 |
June 26, 2025
Rethinking Heavy Equipment Sales in the Digital Age
In this episode of The Construction Revolution Podcast, we sit down with Clement Cazalot of Machinery Partner to explore how they are transforming the way that we purchase heavy equipment. Clement shares how his team is digitizing and streamlining the process of sourcing heavy machinery, making it easier and faster for contractors to get the equipment they need, without the limitations of local sourcing.
We dive into the challenges contractors face when purchasing equipment, and how Machinery Partner’s platform is providing transparent pricing, financing options, and faster delivery times. We’ll also explore the broader impact of digital transformation in construction and the future of the industry. Don’t miss this insightful episode on how innovative solutions are leading the construction equipment industry towards a more agile and efficient future.
PLAY
Episode 55 |
February 27, 2025
Optimizing Concrete from Fleet to Finish
In this latest episode, host Sarah McGuire speaks with Chris Wurtz, Division President at Digital Fleet, about the impact of data-driven decision-making in the ready-mix concrete industry. With expertise in fleet tracking technology, Chris sheds light on the challenges and opportunities of controlling what he calls a “factory on wheels”—the mixer truck. He explores the biggest obstacles facing producers today, from data limitations to inefficiencies in delivery, and highlights untapped opportunities to improve performance. Chris also discusses the vision behind Digital Fleet’s partnership with Giatec on MixPilot and how this integration is helping producers gain better control over their operations. Tune in for an insightful conversation on the future of ready-mix operations and how collaboration between technology providers is driving industry-wide transformation. Don’t miss this engaging discussion!
PLAY
Episode 54 |
February 6, 2025
Smarter Water Management for Safer and Greener Construction
In this episode of The Construction Revolution Podcast, Steven Rossi sits down with Yaron Dycian, Chief Product and Strategy Officer of WINT Water Intelligence. With over 25 years of experience driving strategy and innovation at leading companies like IBM and RSA, Yaron is leading the charge in AI-powered water management solutions. Tune in as Yaron shares the story of WINT, explores the rising challenges of water damage claims, and discusses how advanced monitoring and leak mitigation technologies are shaping the future of construction. From preventing costly damages to meeting sustainability standards and lowering carbon footprints, this episode offers valuable insights into how construction companies can stay ahead in a rapidly evolving industry.
PLAY
Want to Be a Guest Speaker, Sponsor, or Just Have a Question for Us? Fill In the Form!