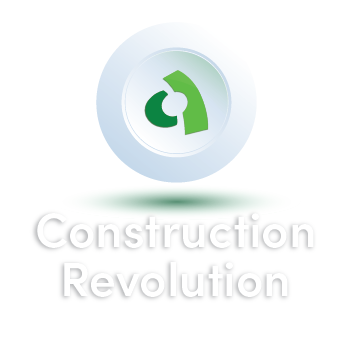
Episode 15 |
October 28, 2021
Building the Robots that Build the World
In This Episode
In this episode of Construction Revolution, Dr. Aali Alizadeh speaks with Phil Cotter, the Head of Deployment Operations at Built Robotics. Phil is helping Built Robotics achieve their mission of “building the robots that build the world”. By upgrading off-the-shelf heavy equipment with AI guidance systems, Built's technology enables machines to operate fully autonomously. Phil brings a unique set of skills and experiences to Built's team that he has gained through his studies of biomedical engineering at Duke University and an MBA at MIT. Phil dives deep into Built Robotics and the technology and products that they are bringing to the market as part of revolutionizing the construction industry.
Host
DR. AALI R. ALIZADEH
Co-Founder & CTO, Giatec Scientific Inc.
Guest
PHIL COTTER
Head of Deployment Operations, Built Robotics
Podcast Transcript
Aali Alizadeh:
Hello there and welcome to the Construction Revolution Podcast. My name is Aali Alizadeh and here on the show, we explore the latest trends, technologies, people, and organizations that are revolutionizing or disrupting the construction industry and are changing the way the industry will look like tomorrow. Today on the show I’m speaking with Phil Cotter, the Head of Deployment Operations at Built Robotics. Phil is helping Built Robotics to achieve their mission of building the robots that build the world. By upgrading off-the-shelf heavy equipment with AI guidance systems Built’s technology enables machines to operate fully autonomously.
Built’s robots are deployed today across the earth-moving industry and they are being used to build critical infrastructures such as wind farms, gas pipelines, and neo housing developments. Phil brings a unique set of skills and experiences to Built’s team that he has gained through his studies of biomedical engineering at Duke University and an MBA at MIT. Phil has spent almost 10 years in the US Army and Special Forces before joining the Built Robotics team.
So again, very nice meeting you Phil and thank you for attending this podcast to chat a little bit about Built Robotics and the technology that you’re bringing to the market as part of revolutionizing or disrupting the construction industry. To begin can you please let us know a little bit about the Built Robotics and some of the products that you were offering to the market in the construction industry in particular?
Phil Cotter:
Yeah, absolutely. So Built Robotics was founded in 2016, we’re a construction technology company that’s focused primarily on transforming traditional heavy equipment into autonomous robots that are capable of conducting autonomous earth-moving tasks on construction sites around the world. So we provide our robots as a service to our partners, and we’re able to collaborate with them to develop the most optimal workflows that work on their particular application and execute autonomous tasks, primarily trenching right now with excavators. But like the long-term vision is certainly to automate different types of tasks on excavators, and then also broaden the scope to other types of earth-moving equipment as well.
Aali Alizadeh:
What are the main pain points that you’re trying to add…as you know, that this is a set of, as you mentioned, robotic additions to existing equipment. What is the challenge that the industry has that you’re trying to solve?
Phil Cotter:
Yeah, for sure. So probably the big elephant in the room is the labor shortage in the construction industry something like 80% of contractors can’t find a sufficient number of skilled heavy equipment operators to be able to conduct the full scope of work. So Built Robotics is able to provide a couple of operational uplifts for our partners. First is from an efficiency perspective, right? You can execute the same dig task, primarily focused on kind of those rote, dull tasks right now, trenching in a straight line for months at a time on some of these job sites, whether it’s in oil and gas or in new energy in wind and solar can be a long laborious time if you’re trenching at the same depth from miles at a time, months and months out. It can be helpful to be able to have a robotic support system to be able to execute those kinds of repetitive tasks.
So from an efficiency perspective partners really see a benefit in terms of being able to execute those tasks to a high quality, like limited rework required, the robot does what you tell it to, right? So that’s the kind of first bit is efficiency and then I think the second bit that’s really important to mention is safety. Those same sorts of repetitive tasks can be long duration and lead to some complacency. And if you can have a robot that just does what it’s supposed to do day in and day out and is highly predictable you can reduce job site hazards and ultimately make a construction site a more safe place to operate.
Aali Alizadeh:
So that’s great to know and so your main product Exosystem is basically the robot that you’re offering and Everest, if I understood correctly is the software or the assist solution behind it. Can you please explain a little bit how these work together to automate the existing machinery on job sites?
Phil Cotter:
Yeah, for sure. So, yeah, there’s a little bit of nomenclature there. So Everest is our software solution. So it lives on a laptop that our robotic equipment operator would be interfacing with. So Everest is kind of the user interface that tells the Exosystem what to do. The Exosystem on the other hand is kind of the hardware component of our kit. So again, we rent robots as a service and the Exosystem is an autonomous retrofit kit that we install on a customer’s piece of heavy equipment. So right now it has a really slick form factor. It looks like a spoiler that hangs off the back of the counterweight of an excavator. And it essentially acts as the brain of the piece of earth-moving equipment.
So you can kind of think about it like the way I like to think about it as the same way a human would hop in the cab, right? They have a number of senses that they use to figure out what’s going on around them and how to plan, what the path of the bucket is going to look like to accomplish their task, right? And then their brain makes decisions on the optimal way to go about accomplishing that task.
And so in the same way, our Exosystem kind of operates as the brain, the decision-making authority as far as you know, how it’s going to track, what the path of the bucket looks like to be able to dig at a specified depth and drop soil at a specified distance from trench edge. And then we also have a suite of sensors onboard as well. So inertial measurement units, and computer vision cameras, RTK GPS that we use to be able to localize the bucket teeth really to less than a centimeter level accuracy. And that allows us to have really, really high-quality trenches at the end of the day which is the name of the game.
So again, we use those sensors to feed into the Exosystem, the kind of brain of the kit. And then our certified robotic equipment operators are able to talk to the robot essentially via Everest, which is the software solution that would live on a laptop that was either in a support vehicle nearby like a pickup truck, or conceivably miles away back in the laydown yard in a trailer. So it provides an operator a lot of optionality, you could even be in another piece of heavy equipment while your robot was executing its dig task. So you can kind of empower an operator to act more like a foreman or a sup in some ways, right? They can be accomplishing a more high-skill kind of finesse judgment-related task that a human is absolutely optimized for while the robot kind of does the simpler tasks.
Aali Alizadeh:
This is very cool, actually. And perhaps with that in mind, the operators that you mentioned as the main value proposition, you mentioned that you’re trying to add a labor shortage in this industry. And now you’re talking about certified robotics operators. Do you envision the same operators or workforce that used to operate these machineries would be trained to use robots, or you can envision, and you said a workforce that would come to the industry that are trained with robotics and they don’t need to have driving skills even or other sites service skills, and they can work with the system and conduct the tasks that previously were conducted by conventional or traditional operators?
Phil Cotter:
Yeah, I think that’s an excellent question and it’s something we think a lot about is who our robotic equipment operators are and how can we ensure that they’re confident, competent, and capable to operate the system in an industry that’s as operationally-intensive as construction, right? So in much the same way that you had to train operators to learn how to use hydraulic excavators when those entered the market, then with machine control and kind of the integration of some GPS support that a lot of the manufacturers now offer as well you have to be trained how to use that in addition. So we’re very thoughtful about what our certification pipeline looks like and so we’ve constructed some online training and then importantly a dedicated block of in-person instruction where a Built instructor kind of transforms, whether it’s an operator or a surveyor or a grade checker into a Built certified robotic equipment operator.
We think it’s incredibly important that that is a deliberate effort as well, because ultimately, like we said, one of the key benefits here is that it’s safe. And also that we’re providing a meaningful operational benefit to our partners as well. It’s actually a good opportunity to kind of note our five-year partnership with the International Union of Operating Engineers as well. So we’ve been working closely with the IUOE to develop a certification pipeline so that operators can now learn this additional skill and have an additional tool in their tool belt, right. So that they can leverage this appropriately for whatever the task is that the partner wants to accomplish.
So the nice thing about Everest specifically is that it’s a program that was designed in 2021, right now. So it doesn’t look like a traditional like factory automation human-machine interface, right. It’s a nice slick, totally intuitive interface that you use to be able to transform an excavator into something that can operate autonomously. And so pretty quickly we can take someone who’s comfortable on a job site and make them a capable REO or robotic equipment operator in about a week, and they can be out there providing value on the job site with this new tool.
Aali Alizadeh:
Awesome. So your robotic system, Exosystem combines obviously set of sensors that you mentioned and software and the backend to there was artificial intelligence trying to understand data and make decisions. Do you see the AI making decisions on its own in critical situations or do humans need to be there to override? How do you see the combination of human-based decision-making and the artificial intelligence space decision-making?
Phil Cotter:
Yeah. I think that this kind of like integration is something that we also think about quite a bit, right? The robot is smart. It can do what you tell it to very capably and you can walk away from it and end up with a very high-quality trench kind of overnight or operating 24/7. But if the robot gets stuck, sometimes it needs a hand, right? So because of the way we have Everest designed and because of the… We have another system called Guardian that kind of is always on call monitoring the robot as well. It will basically pause itself when it decides that something off-nominal is happening that it can’t get out of. And so that actually highlights what I think is one of the key strategic design decisions that Built Robotics made kind of at the advent of this retrofit solution, which was to preserve the ability to still put an operator in the cab of this piece of equipment.
So at any time the REO can pause the robot’s operations, hit the emergency stop button, enter the cab and be able to kind of investigate whatever the robot has notified the REO has happened, or to do some kind of high skill judgment type requiring task, and then can hop back out of the cab and simply press play again, essentially and the autonomous operation can resume. So we think it’s really important that you can still… Excavators are kind of like multi-tools on many construction sites, right? They do a number of things. They don’t just do trenching, right? So being able to throw an operator in the cab have them either get the robot out of a situation that it’s told the REO that it’s in, or be able to pull it off to go pull cable or lift something or do whatever other task is required is something that we think is really important.
Aali Alizadeh:
This is great. I think there was a statement on your website that there has been zero injuries so far from robots. And this is fantastic that you’ve thought about all the safety features and the aspects that you need to implement to ensure a smooth operation that humans can trust from the robotics perspective. But when you approach potential customers to integrate Exosystem with their existing machinery, I’m sure like any other technology adoption there’s always a lot of questions and hesitancy. What are the main questions that you get from potential customers about adopting something as sophisticated as your technology?
Phil Cotter:
Yeah, that’s another good question. I think like any new technology, especially in an industry that’s as operationally intensive as construction, there can be some hesitancy initially, and it’s understandable, right? Downtime is money on a construction site. So I think the first-order questions are generally around how this is going to integrate on my job site, right? What kind of production rates can I expect? What are the other support requirements that I need to provide? And I think we’ve been on nearly 20 commercial job sites right now. We’ve been on some enduring job sites that have been ongoing for more than a year at this point in time. So we have some real valuable on-the-ground experience. This isn’t something that just works in a testing yard in San Francisco right now.
So there’s different buckets of adopters, right? You have early adopters who are very excited to be able to get this on their job site immediately. And then you have some folks kind of in the middle who want to wait to see that it works first. And I think I’m super excited now because I think that we’re really starting to get into the meat of customers who can see this. They’ve seen it work on solar sites, on oil and gas sites and are eager to go ahead and integrate it. I think we’re able to deploy pretty seamlessly at this point and have some best practices as far as what our requirements are and making sure that we’re getting set up efficiently and moving dirt kind of as quickly as possible.
Aali Alizadeh:
Is your system compatible with a wide range of equipment that is out there from different manufacturers or you specifically design your system for one or few type of these machines out there?
Phil Cotter:
Yeah. That’s another great question. So essentially we can retrofit any type of late model excavator. So basically anything that’s electric over hydraulic makes it very easy for us to come and retrofit that piece of equipment. So whether you’re running CAT, Deere, Hitachi or whatever else we can come in and basically run a three to four hour installation and calibration process. And we can calibrate different buckets that you might use so that you can simply select them from a dropdown menu in Everest. And then I think it’s also important to note too, that it’s a fully reversible retrofit, so there’s no welding required. You get your excavator back the way that you gave it to us before you retrofitted it.
So definitely I think that’s one of the other key values here is that you don’t have to be married to a specific type of equipment in order to see the value of this autonomous retrofit. You can be operating autonomously with whatever type of excavator you have following that three to four hour installation and calibration process.
Aali Alizadeh:
Great. Yeah. So as a customer, as a potential customer, if I want to get a start at with your technology hardware and software in the US, Canada or other countries how should I go about it?
Phil Cotter:
Yeah. So there’s a place on our website you can come drop us a note and we’d be happy to hop on a call with you and discuss kind of what the best usage would look like. And we’re not… While we’re focused on trenching right now certainly like I said before the intent is to get back to other types of earth-moving activities as well. So the kind of flow looks like you reach out to us, we’ll discuss kind of what our solution looks like and how we can optimally kind of integrate with your workflow. And then we’ll come out to your site with an Exosystem and a Built certified technician will do the retrofit, do the installation and calibration.
We can run your candidate robotic equipment operator through our certification pipeline, and you can be moving trench autonomously or moving dirt autonomously within a day. So you’d be able to execute that task for as long as you’d like, and then kind of at the end of whatever that task is, whether we’re talking about weeks, months, or years, we can recover the Exosystem and you still have your traditional piece of heavy equipment after the fact.
Aali Alizadeh:
At this point, what type of equipment do you automate? Is it more on the excavation side of things where you have a wide range of activities that you can automate using your robots?
Phil Cotter:
So in the past, we’ve done everything from compact track loaders to dozers to excavators. And right now we’re focused on trenching with excavators, but kind of like I talked about before too an excavator is a nice place to focus because an excavator does a lot of things on a job site. And so with this hardware and software solution, you know our hardware is robust enough to kind of be enduring for whatever task you might want to do. And then beyond that it’s software essentially. And that’s kind of what Built is. That’s Built bread and butter, right? Is building the software that kind of does the decision-making, the controls, the perception to be able to prescribe an earth move, whatever that task is kind of optimally.
Aali Alizadeh:
Now, I have a general question and job sites are in a way similar to war zones to some extent. There’s a lot going on, there’s a lot of different activities, machinery equipment, people coming and going. It’s one thing to imagine these robots work in a separated standalone environment whereas in a real big job site you have multiple machinery, equipment, people, activities. How do you ensure that these machines in that sort of environment would work the way that you have designed them in a standalone operating mode? You know maybe you can bring up some of your experience from Special Forces and how you plan these kinds of different scenarios and the plan that you give to the robot to do a trench is great at the beginning, but during that time a lot of things changed on the job site. People bring additional equipment, remove things, and the scenario would change. How do you ensure the robot would understand that and operate or continued its operation safely during the whole period of the project?
Phil Cotter:
Yeah, sure. So as you indicated, I have some experience solving some operational problems in kind of high-risk environments and construction is a high-risk environment, I think. Anything you can do to kind of mitigate and squeeze out the risk on a job site to try and make it safe and be able to ultimately build what you hope to build is value in my mind. And so Built really believes that there is no amount of productivity that means anything if you’re increasing the risk on a job site. So we think about safety really deliberately. Understanding all the moving pieces that you talked about as well.
So kind of our safety architecture we bring a layered approach to that. So from Everest, you can pause or stop the robot at any point in time, you can view all the cameras that the robot has so you get a good 360-degree view of what the robot sees and what’s going on around it. And we have Guardian on call that’s monitoring kind of as a backstop as well. So you’ll get a notification if the robot sees an obstruction or an obstacle or runs into some kind of issue that it needs help getting out of. We also have pedestrian detection on board so as you kind of get closer, we’ve trained it on many hours of construction video. So we’re very good at recognizing people with PPE and so that’s a helpful backstop as well. The robot will put itself into a pause mode, and if it detects a dismounted person within an unsafe distance. We also have wireless E-stops that are located at the safety stations nearby the robot as well.
So any passer-by can come by and hit an emergency stop and put the robot into a safe mode and pause its operations if it’s doing something unsafe. There’s also a physical safety barrier that we put around the robot as well. So it’s like waist-high, high visibility tape that stands out on a job site. And it’s nice too because most job sites have kind of a colored tape operating procedures, so people who are there are sensitive to the idea of not crossing tape. The robot’s also geo-fenced. So geo-fence maps to the safety barriers so it’s very clear what the sandbox is essentially, that the robot is able to play inside of.
There’s also lights and sounds. So if you hear slow beeps and you see constant blue lights, you know the robot’s safe to approach. If you see flashing blue lights or fast beep or hear fast beeps, you know the robot’s in autonomous mode and it’s unsafe to approach. And then kind of the final layer of defense are hardwired E-stops that are on the robot as well. So for whatever reason and this wouldn’t happen, but if it did move you could have to those hardwired E-stops as well. So we think very seriously about how we make sure that a 90,000 pound piece of heavy equipment is not doing something unexpected and there are multiple ways to make sure that it is safe.
And I think that’s absolutely critical, right? Because like I said from the beginning, there’s no amount of productivity that matters if somebody gets hurt on a job site. So thinking back from my time in the army, I think that that is true as well. You try to squeeze out as much risk as you possibly can so that then you can focus on the task that matters, which is moving dirt the way that you want to move dirt.
Aali Alizadeh:
Awesome. It seems that you have thought about all the details and different aspects of getting this technology safely deployed in job sites and which is great to hear. As jobs are getting more automated with the introduction of sensors, IoT, concrete sensors, all the types of robotics in the field, and obviously automating multiple machinery and equipment on the job sites. Do you envision these automated equipment sensors would communicate with each other, multiple equipment talk to each other or they at least detect maybe people with trackers on them or IoT networks in job sites so that they can together automate things beyond even the equipment main purpose?
Phil Cotter:
Yeah. So I think definitely the vision is that you could have one robotic equipment operator supervising the autonomous operation of multiple different robots at the same time. So whether that was multiple excavators trenching at the same time, or whether that was doing some kind of loading operate, load and haul operation you can kind of envision as you widen out from trenching, what all the different kind of spectrum of options are. And you can leverage our technology to be a force multiplier for your operation. Not only can you take one individual and make them capable of supervising a robot while they do something else or supervising multiple robots, but you can also get a lot of kind of project managerial benefits from having a robot on your site.
You know down to the centimeter how much trench was produced today, what the production rate of the robot is in this specific soil condition at this specific depth. You get a lot of good metrics that would just be, frankly, kind of harder, onerous to get without a robot kind of out there doing that. So it allows you to plan those follow on operations that you need in order to kind of accomplish the ultimate goal of the construction task that you’re doing, because rarely are you just opening a trench to open a trench, right? You’re laying some kind of infrastructure and whether it’s cable or pipe or what. So there’s a lot of benefit to being able to pull those metrics off. And then as you start to expand to other types of equipment and other types of more complex dig tasks that require multiple pieces of equipment, or kind of dismounted human teams operating nearby you can integrate those things even better from a project managerial perspective.
Aali Alizadeh:
Perfect. Now technology is advancing at a very fast pace, and I’m sure you’re working on the next generation of your products. And then if you can share with us what the future holds for Built Robotics, so you envision self-driving concrete trucks or automating concrete operations, or other types of equipment in job sites, if you can share with us, that would be great.
Phil Cotter:
Yeah. I mean we think Built Robotics is going to be the next big thing since hydraulics, right? We hear a lot about autonomous self-driving on roadways and we’ve come a long way from factory robots that are in cages and on manufacturing lines, right? So I think being able to put robots on job sites, again, across multiple different equipment types across multiple different types of earth-moving tasks, and have them be able to collaborate and kind of optimize their work in a kind of a collaborative way, really could see some massive operational benefit for our partners.
And so, frankly, I don’t think we’re very far away from doing that. The next generation of our hardware is in the pipeline right now and the next generation of software is being launched kind of as we speak. So I think as we dial that stuff in, it’ll really open up a world of possibility for these other types of applications and kind of that cooperative kind of like team-based approach to earth-moving. And we’ll really be able to see what this next step looks like in the construction industry here in the very, very near future.
Aali Alizadeh:
Thank you so much, Phil for sharing what Built Robotics is doing in the industry and this is very fascinating and great to see that the construction industry is getting revolutionized by a different type of technology, now in the hands of robots and they’re automating very simple yet sophisticated tools or activities that we have been doing for a long time in this industry. Do you have any additional comments or feedback for our audience to know about Built Robotics and what you’re bringing to the market?
Phil Cotter:
Yeah, I mean, I think I would end with we learn we’re not construction experts, right? Our partners are the construction experts, we’re providing a new tool that they can use to be able to operate more efficiently and more safely. And every time we go out a job site, we come back with key insights about stuff we didn’t realize or didn’t understand how to prioritize differently for a specific application. So always eager to connect with folks who are using different applications in different verticals or are looking to try something new because we have the benefit of being able to incorporate and iterate pretty quickly. So please don’t hesitate to reach out if you’re interested in learning more about what Built Robotics does and how to conduct autonomous earth-moving tasks on your dig site.
Aali Alizadeh:
Awesome. Thank you so much again for your time, Phil and sharing experience that you have at Built Robotics with us.
Phil Cotter:
Awesome. Thank you.
Other Related Episodes
Episode 55 |
February 27, 2025
Optimizing Concrete from Fleet to Finish
In this latest episode, host Sarah McGuire speaks with Chris Wurtz, Division President at Digital Fleet, about the impact of data-driven decision-making in the ready-mix concrete industry. With expertise in fleet tracking technology, Chris sheds light on the challenges and opportunities of controlling what he calls a “factory on wheels”—the mixer truck. He explores the biggest obstacles facing producers today, from data limitations to inefficiencies in delivery, and highlights untapped opportunities to improve performance. Chris also discusses the vision behind Digital Fleet’s partnership with Giatec on MixPilot and how this integration is helping producers gain better control over their operations. Tune in for an insightful conversation on the future of ready-mix operations and how collaboration between technology providers is driving industry-wide transformation. Don’t miss this engaging discussion!
PLAY
Episode 54 |
February 6, 2025
Smarter Water Management for Safer and Greener Construction
In this episode of The Construction Revolution Podcast, Steven Rossi sits down with Yaron Dycian, Chief Product and Strategy Officer of WINT Water Intelligence. With over 25 years of experience driving strategy and innovation at leading companies like IBM and RSA, Yaron is leading the charge in AI-powered water management solutions. Tune in as Yaron shares the story of WINT, explores the rising challenges of water damage claims, and discusses how advanced monitoring and leak mitigation technologies are shaping the future of construction. From preventing costly damages to meeting sustainability standards and lowering carbon footprints, this episode offers valuable insights into how construction companies can stay ahead in a rapidly evolving industry.
PLAY
Episode 53 |
December 12, 2024
Unlocking AI’s Potential in Construction
In this latest episode, host Sarah McGuire sits down with Sean Devine, Founder and CEO, XBE, to explore the transformative role of AI in the construction industry. With a background in logistics and technology, Sean brings unique insights into the challenges and opportunities surrounding AI adoption in construction. Sean highlights untapped opportunities and discusses how XBE is leading the charge with innovative solutions, including AskConcrete— a groundbreaking answer engine powered by decades of NRMCA data, designed to tackle complex questions about ready-mixed concrete. From identifying industry limitations to exploring what companies need to do to embrace AI effectively, Sean offers a compelling roadmap for innovation. He also shares his journey in founding XBE and his mission to optimize heavy construction operations with cutting-edge technology. Tune in to gain valuable insights into how AI is shaping the future of construction. Don’t miss this enlightening discussion!
PLAY
Want to Be a Guest Speaker, Sponsor, or Just Have a Question for Us? Fill In the Form!