How to Improve Construction Cost Control From Pre-Planning to the Jobsite
Cost control in construction is a business decision, just like choosing the right project. Each job influences cash flow, profitability, and how your company is perceived in the market. Taking on work is not only about technical capability or capacity. It is also about whether the financials add up, the risks are acceptable, and the project supports your long-term goals. Managing costs with discipline ensures that these decisions lead to real returns. When done well, it strengthens planning, reduces financial risk, and gives clients confidence in your ability to deliver. It depends on accurate data, clear reporting, and steady coordination between the office and the field.
With the right systems and habits in place, you can keep projects on track, build lasting trust, and stay competitive in today’s construction industry. Learn how to improve cost control across every phase, from the pre-planning stage to the jobsite.
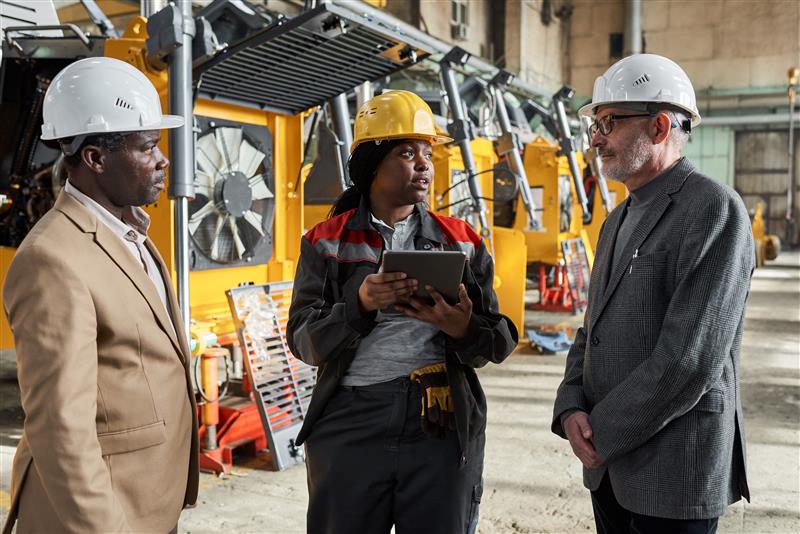
What Is Construction Cost Control?
- Creating accurate budgets
- Monitoring costs throughout the project
- Managing changes as they happen
- Making timely decisions based on field data
Why It Matters
- Improve forecasting
- Increase transparency with clients
- Strengthen bid accuracy
- Protect profitability
The Bigger Picture: Cost Control as a Business Strategy
Cost control does more than keep individual projects on track. It shapes how construction businesses manage uncertainty, protect margins, and stay competitive across multiple jobs and teams.
Risk Management Starts with Visibility
Regularly comparing actual costs to planned budgets helps teams spot financial risks early. When issues like material shortages or price increases are identified in time, teams can adjust their approach before those risks affect the schedule or bottom line.
Protecting Margins Through Smarter Planning
Regularly comparing actual costs to planned budgets helps teams spot financial risks early. When issues like material shortages or price increases are identified in time, teams can adjust their approach before those risks affect the schedule or bottom line.
Clarity That Keeps Teams Moving
When cost data from the field is available to everyone—not just the office—project teams can respond faster. Shared visibility helps avoid delays caused by miscommunication or outdated reports and allows decisions to be made with confidence.
Turning Performance into a Competitive Advantage
Consistently delivering projects on time and within budget builds a reputation for reliability. That reputation helps secure repeat clients, improves the chances of winning new bids, and supports long-term growth.
Common Challenges That Disrupt Cost Control
Even experienced teams encounter issues that affect cost control.
Challenge | Impact |
Outdated estimates | Leads to budget shortfalls when recent price hikes or supply changes aren’t reflected in planning. |
Delayed expense entries | Create a false sense of financial progress and make it harder to spot overruns early. |
Incomplete field reports | Omit key labor or material costs, reducing the accuracy of real-time tracking and forecasts. |
Untracked scope changes | Results in budget and schedule creep that aren’t captured until it’s too late to correct. |
Disconnected systems | Prevent timely data sharing between the field and office, making oversight and coordination difficult. |
Slow approvals | Stall procurement and on-site decisions which can cause idle time and increase labor costs. |
Scheduling gaps | Cause crews or equipment to wait unnecessarily, driving up indirect costs and reducing productivity. |
Market shifts | Unexpected changes in pricing or availability impact procurement and throw off original budgets. |
Regulatory changes | Introduce new compliance costs that weren’t factored into initial financial planning. |
Inconsistent coding | Makes cost data hard to analyze, which limits insights into where money is actually going. |
Addressing these issues takes more than tools. It requires a consistent process, timely data, and active team coordination.
Creating Detailed Line-Item Budgets
High-level budgets make it difficult to identify problem areas. A line-item approach gives teams more visibility and control.
- Break down costs by category: labor, materials, equipment, subcontractors, and overhead
- Organize costs by task or phase
- Link budget lines to schedules and procurement plans
Update budget actuals regularly. Reconcile invoices to catch overruns early. Use templates to keep reporting consistent.
Practical Ways to Strengthen Cost Control
Cost control improves when teams stay consistent in how they plan, track, and respond to changes. Adding structured forecasting and life cycle planning takes this further.
- Use current data when estimating. Work with recent pricing and supplier input.
- Apply forecasting tools like Earned Value Management (EVM). EVM links project progress with both budget and schedule to reveal risks early.
- Structure your cost breakdown. A clear Cost Breakdown Structure (CBS) helps track performance by category.
- Use Life Cycle Cost Analysis (LCCA). This evaluates long-term material and maintenance costs, helping to balance upfront pricing with durability.
- Centralize documentation. Keep all reports, changes, and expenses in one place.
- Train your staff to understand cost data. Ensure that teams can act on what they track.
These strategies help teams shift from reacting to problems to preventing them.
Analyze Variances and Track Trends
Comparing estimates to actuals helps identify risks.
- Cost variance shows how spending compares to budget
- Schedule variance tracks timeline performance
- Resource variance reveals labor or equipment gaps
Use visual dashboards to monitor trends and guide decisions.
Managing Change Orders Effectively
Change orders can disrupt costs and schedules. A clear process reduces risk.
- Document changes with standardized forms
- Secure approvals before beginning work
- Update budgets and timelines promptly
- Keep all stakeholders informed
Use centralized logs and digital tools to maintain clarity and transparency.
Building Contingencies into Cost Planning
Unexpected issues happen. Contingency planning prepares teams to respond effectively.
- Allocate funds by complexity and phase
- Track risks with a register
- Prioritize using a probability-impact matrix
- Review and adjust regularly
Contingency funds should be visible, intentional, and reassessed throughout the project.
Improving Stakeholder Communication
Clear communication helps teams manage costs and expectations.
- Identify key stakeholders: owners, subcontractors, suppliers, and finance teams
- Share updates through project platforms
- Use summaries and visuals for reports
- Hold regular meetings to review cost status and updates
Good communication strengthens coordination and avoids confusion.
The Role of Technology in Cost Management
Technology improves how teams manage and monitor costs. In concrete construction, the right tools can support everything from concrete mix efficiency to financial reporting.
- Remote concrete monitoring lets teams track curing and strength progress in real time. This supports faster scheduling and reduces the need for extra testing.
- Building Information Modeling (BIM) supports better design coordination, detects clashes early, and improves material tracking.
- Enterprise Resource Planning (ERP) systems connect cost tracking, procurement, and scheduling, helping teams manage cash flow and align field activity with financial goals.
The best tools are those that support daily workflows and give teams the information they need to make fast, confident decisions.
Making Financial Goals Part of Field Decisions
Cost control depends on what happens in the field just as much as in the office. Many of the decisions that affect the budget are made on site through scheduling, resource use, and material handling.
To keep costs under control, field teams need access to timely, accurate information. When real project data is used to guide day-to-day decisions, teams can respond quickly and avoid small problems turning into larger overruns.
Here are a few ways this connection makes a difference:
- Concrete strength data collected from the field helps determine when to remove formwork, start follow-on trades, or reschedule inspections. These choices can save both time and labor costs when based on actual performance rather than fixed timelines.
- Higher-than-expected material use may point to issues like batching errors, overdesign, or poor forecasting. Identifying these trends early allows teams to adjust before costs accumulate.
- Shifts in site conditions, such as changes in temperature or delays in curing, can affect timing and resource allocation. Having up-to-date data allows project managers to make informed changes without derailing the budget.
Aligning field activity with financial goals gives teams more control over how a project unfolds. Instead of waiting for reports to confirm a problem, teams can act with confidence and stay ahead of schedule and budget targets.
Efficiency Supports CO2 Reduction
Strong cost control often leads to better environmental outcomes. In concrete construction, efficient practices reduce waste, lower emissions, and improve long-term project performance.
Efficiency Supports CO2 Reduction
- Optimizing mix designs helps lower cement content while still meeting performance targets
- Using less cement cuts material costs and decreases carbon emissions
Avoid Rework
- Consistent batching, accurate testing, and reliable scheduling help prevent errors that lead to repours
- Fewer mistakes reduce material waste, labor hours, and energy use
Eliminate Overdesign
- Designing only what is required prevents overuse of concrete and reinforcement
- This improves both cost performance and sustainability outcomes
Improve Scheduling and Curing
- Real-time data helps guide decisions on curing timelines and formwork removal
- Smarter planning limits downtime and lowers resource consumption
Support Financial and Environmental Goals
- Efficient processes support both budget targets and sustainability goals
- Teams can meet performance expectations while minimizing waste
By focusing on efficiency from the beginning, construction teams deliver results that support both project outcomes and long-term environmental responsibility.
How the Giatec Ecosystem Supports Cost Control
Giatec’s concrete monitoring solutions are designed to help construction teams make smarter, faster, and more cost-effective decisions throughout the concrete lifecycle. By combining field data, mix optimization, and real-time analytics, the Giatec ecosystem improves cost control in four key areas:
1. Smarter Mix Design
Giatec SmartMix™ uses artificial intelligence to optimize concrete mixtures based on performance goals, material constraints, and field results. It helps reduce cement overuse, lower material costs, and limit the risk of overdesign, without compromising strength or durability.
2. Real-Time Strength Monitoring
SmartRock® wireless sensors provide continuous data on in-situ concrete temperature and strength through the maturity method. This eliminates the need for frequent break tests and allows teams to strip formwork, schedule pours, or move to the next phase sooner. Reduced waiting time translates to lower labor and equipment costs.
3. Centralized Reporting and Insights
Giatec 360™ gathers sensor data and delivers visual dashboards that track performance, identify trends, and support proactive planning. Project managers can spot anomalies, review progress, and align field activity with the budget in real time.
4. Improved Batch Quality
MixPilot™ monitors batching performance and adjusts inputs as needed during production. This leads to more consistent results, fewer rejected batches, and less wasted material.
By connecting mix design, field performance, and reporting in one ecosystem, Giatec gives teams the visibility they need to reduce delays, limit material waste, and stay within budget. These tools support more accurate forecasting, stronger planning, and better decision-making at every phase of the project.
Case Study: Using Data to Optimize Mix Design and Reduce Material Costs
During the Harrah’s Cherokee Casino Resort project in North Carolina, Whiting-Turner used SmartRock sensors to monitor in-place concrete strength in real time. The data showed that their concrete mix reached 3,000 PSI in just four hours, which was significantly faster than expected.
With this insight, the project team worked with their concrete supplier to adjust the mix design. They were able to reduce the amount of cement and additives while still meeting strength requirements. This optimization resulted in savings of about $4 per yard, adding up to nearly $40,000 in material cost savings over the course of the project.
Real-time strength data also helped the team remove formwork earlier and coordinate trades more efficiently. While the case study does not assign a specific dollar value to those improvements, the labor and scheduling benefits were clear.
This example illustrates how timely field data and technology can lead to smarter material use and more efficient decision-making in concrete construction.
Conclusion
Embedding cost control into daily workflows improves consistency and reduces the risk of unexpected overruns. It depends on clear planning, timely field data, and tools that allow project managers to respond before issues turn into delays or budget overruns.
Targeted improvements in mix design or sequencing often produce measurable savings in both labor and materials. Access to real-time data allows teams to make confident, timely decisions that directly impact project cost and efficiency. Most importantly, it helps build trust and lasting relationships with clients.
Construction teams that invest in integrated systems and consistent cost tracking set themselves up for stronger performance. Over time, this approach leads to more reliable delivery, better margins, and projects that meet both financial and operational goals.
With a consistent approach, cost control becomes a tool that supports smarter, more sustainable, and more successful construction from start to finish.
Jump to the section
- How to Improve Construction Cost Control From Pre-Planning to the Jobsite
- What Is Construction Cost Control?
- Why It Matters
- The Bigger Picture: Cost Control as a Business Strategy
- Common Challenges That Disrupt Cost Control
- Creating Detailed Line-Item Budgets
- Practical Ways to Strengthen Cost Control
- Managing Change Orders Effectively
- Building Contingencies into Cost Planning
- Improving Stakeholder Communication
- The Role of Technology in Cost Management
- Making Financial Goals Part of Field Decisions
- Efficiency Supports CO2 Reduction
- How the Giatec Ecosystem Supports Cost Control
- Case Study: Using Data to Optimize Mix Design and Reduce Material Costs
- Conclusion