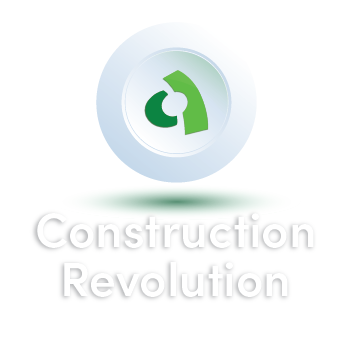
Building Better With AI - Episode 3
Episode 40 |
April 18, 2024
The Realities of Mix Optimization
In This Episode
In this third episode of the “Building Better with AI” mini-series, host Sarah McGuire leads an insightful discussion on “The Realities of Mix Optimization” with the distinguished Heather Brown, Ph.D., VP, Quality Control and Quality Assurance, Irving Materials.
Delving into the educational realm of the concrete industry, the conversation contrasts classroom teachings with the dynamic challenges of real-world applications. Dr. Brown sheds light on the fundamental shifts she’s observed in industry perspectives over the years, unveiling the evolving nature of optimization.
Throughout the episode, Sarah and Dr. Brown confront current challenges, from navigating diverse markets to limitations in testing practices, and discuss the need for evolving methodologies. Drawing from her extensive experience, Dr. Brown highlights the potential of AI in bridging these gaps and empowering informed decision-making.
Don’t miss this insightful episode delving into the intricacies of mix optimization. Tune in now and gain valuable insights into enhancing your concrete practices!
Host
Sarah McGuire, MBA
AVP, Business Development, Giatec Scientific Inc.
Guest
Heather Brown, Ph.D.
VP, Quality Control and Quality Assurance, Irving Materials
Podcast Transcript
Sarah McGuire:
Hello concrete revolutionaries and welcome to the third episode of Building Better with AI. I’m your host, Sarah McGuire, and today we’re going to be discussing the realities of concrete mix optimization in past and present day. I’m joined here by Dr. Heather Brown, who has served as the director and professor at the School of Concrete and Construction Management at Middle Tennessee University for 20 years. In 2021, she embarked on a new chapter as the vice president of quality control and assurance at Irving Materials. Notably, she was recognized for her outstanding contributions to the industry and the prestigious Champion Award by the Concrete Industry Management National Steering committee during the organization’s special 25th anniversary. Heather, thank you so much for joining me today.
Dr. Heather Brown:
Thank you, Sarah. I’m excited to be here and thanks for the introduction.
Sarah McGuire:
Heather, you were on an episode of the Add 10 Gallons podcast a couple of years ago where you really dove into the background of the founding of the CIM program, how you got into this industry, and even the female experience, which I found really interesting. We have a lot to dive into today on the actual topic, so I’m actually going to ask that we put a link into the description of this podcast so that if anyone wants to listen to that after. But I do just want to ask you one question to get us started. What do you love about concrete and what gets you the most excited about the industry today?
Dr. Heather Brown:
That’s a great question and probably a pretty loaded question because I loved concrete for so long. I really discovered it as a sophomore in college and it was just so exciting to think that you could change one material, one dosage rate, one temperature, and you had a completely different mix. So when I was an educator, I would talk to a lot of young people about concrete and I would liken it to cooking. Just one change in the recipe and you’d get a whole new batch of cookies. And I think that that passion has stayed with me this entire career because truly that is what concrete is to society. It’s a different recipe for different applications, for different needs. And we can be custom, almost like custom paint colors. We can be so custom in how we serve society and I think that that’s such an exciting thing to get behind. And then all the challenges that we face with those material changes just creates a whole new energy and passion of, all right, we’ve got a new challenge, let’s work on this. So I think that to me is what keeps me excited about the material. I love all of the other construction materials and I think that there’s a place for each of them, but concrete just always, for me, was at the top of the stack for creativity, innovativeness and really what was going to take our society into the future.
Sarah McGuire:
That’s really interesting because obviously we have a lot of civil engineers here in our office as well, but usually concrete is the one thing that they all come into after school and they say it’s the least common thing to learn about. There’s just not enough education around it. But then at the same time, that means there’s so much room for innovation because we haven’t been spending enough time on it. And of course, the reason I thought you were going to be a perfect fit to talk about this topic today on optimization is because you have that experience of being in academia and now you’ve got the experience of going into the private sector and seeing the parallels there. Our founders actually, they also spent a long time in academia and research, but then when they started to innovate they said, we don’t want this to get stuck here. We want to actually bring it to the practical world. So I’m really interested to hear what’s been the biggest adjustment for you in going from this world of academia, which has a lot more practical components than I think most programs probably would. But what’s been the biggest change in jumping from one to another?
Dr. Heather Brown:
I do think that when I was in academics, I really did try to have a pulse on what was going on in the real world and I worked really hard to bring that to the classroom. So I feel like I had a little bit of a headstart when I was considering going back into “the real world” in the private sector. But the pace. I think the pace has been the biggest challenge. I love troubleshooting. I love problem solving.
But the pace that this industry commands and demands that amount of energy is relentless. I really do think though that it’s as much exhausting as it is rewarding because I do see people wanting good change and I do see people wanting to find these best practices and change cultures. And to be able to slip in and help a company and an organization and an industry do that wearing my teacher hat still, but then also learning and growing alongside with them shoulder to shoulder has been awesome. But the pace is … My week might be completely planned out on my calendar, but one afternoon can upturn the entire week. I think that’s what I’ve learned in the short time I’ve been with IMI. Two and a half years, and I couldn’t tell you what all we’ve been able to accomplish in two and a half years because it was just a constant movement, constant change, constant analysis of are we doing the right things.
Sarah McGuire:
That’s really interesting. It’s going to feel like I seeded that question to you or seeded that answer because that need to react so quickly in this industry is a huge reason as to why technology can really help us bridge that gap. There’s a lot of fear around technology. Oh, it’s going to take my job and it’s going to replace the need for this. But there’s actually a lot that it can do to supplement that so you can focus on the problem solving, which I think people are craving to do, especially the younger generation that you’ve been teaching and you are a part of yourself. What made you decide to make the change?
Dr. Heather Brown:
Well, I think when I got into academics, that was an unexpected turn. I wasn’t planning on getting the PhD to actually pursue being a professor. I was getting it to be in the consulting material testing world. So the passion to on this side of the fence had been there from the beginning. I was lucky … You mentioned that there’s not a lot of concrete taught in college and there’s not. To this day, civil engineering does not put enough emphasis on concrete. However, I was fortunate in that one of my professors was a retired DOT professional and he loved concrete. So I was fortunate in that I learned so much from him. So I guess I got an early peek into what really material testing and optimization and looking at innovation, what it was going to be like. And so my passion was set. I wanted to be in material testing for life, but I really just got lucky in that there was this program starting up and I was able to jump into the academic side and really hone my skills there.
It’s a very safe space to hone your material testing background and you can do research and you can make mistakes and nobody’s charging you dollars to make these mistakes. You’re really able to foster young people and their passion for R&D and then your own passion for what’s possible. How can I make things better? And then you go to ACI and ASTM and you bounce your ideas off people. Again, very safe spaces. So I feel fortunate that I was able to hone those skills for 20 years, but then once I jumped into the ready mix business, I realized there is a outcome for every little decision. That outcome might affect production, it might affect safety, it might affect sales. And so now I’m having to pay attention to the whole pie, and I really do feel like that’s what I was missing as an academic is understanding that whole pie.
So I feel fortunate that I can put all those pieces together financially, schedule, how it impacts contractors and really help the industry solve problems holistically and not just from that very narrow lane of material optimization. But to your point, there’s still a lot of manpower required to gather all that information. And I feel fortunate that we have this great quality control team that helps me gather the nitty-gritty data that I need in order to be able to make wholesale changes to what we’re doing as an operation. And without that boots on the ground, we can’t get it done. There’s no computer that’s going to go and talk to a contractor and get that feedback to then look at how can we make adjustments. Now, lots of data does need a lot of automation, and so I think where technology steps in is it can process and automate and analyze a lot more data than we can individually. So it’s a compliment to what we do versus a replacement to what we do.
Sarah McGuire:
So knowing what you know now after being in the private sector for a couple of years, would you go back … And you probably are already in touch. But would you go back and say there’s one class that we really need to add here to prepare anyone?
Dr. Heather Brown:
CIM is a little unique in that its curriculum is already very in touch, I think with what industry needs. But I do say to myself quite often, oh, I would be a such different teacher if I could go back and input some more just really real world scenarios. I think that’s what it is. It’s about experiential learning versus just textbook learning. And I felt like we empowered the students to feel confident that they had translatable skills to get into ready mix or precast or construction right away. But I almost feel like there’s tenfold examples I could give them now of how they could be boots ready. What can I tell them to get them even more prepared to face the fire? Because your hair’s on fire every day. So how do I help them know that’s coming and then also give them tools to solve problems a little faster without feeling like they’ve got years of in-person experience to be able to be valuable to their company?
Sarah McGuire:
Right. Are there any courses that are really structured around new technology advancements?
Dr. Heather Brown:
I think what we try to do when I was a professor … And I’m still a part of the CIM network. I’m in charge of their education committee now, so I serve at the national steering committee level. So that was fun for me because now I get to help the directors and the professors stay current. And so when we talk, when get together, we do bring up new technologies a lot. Because how do you find space in the curriculum that has been well-built very robust, is doing a good job, but knowing that we’re going to miss the boat if we don’t introduce all of these new technologies because the students are going to be faced with that right when they take their first position. So we interview students a lot after they come back for their internships. “Hey, what’d you see? What’d you learn?” And make sure if they’re learning it at the internship level, we need to put it back in the curriculum because that means it’s here and they need to understand it. So it’s just the unfortunate part is trying to fit it into a set 120 hour curriculum.
Sarah McGuire:
But you do have … It sounds like the internship component is very, very pivotal to that. Even I started at Geotech nine years ago tomorrow actually as an intern and then they couldn’t kick me out after. They took me to World of Concrete. I saw everything around me and I went, wow, this is way more than I would’ve expected from an industry that I knew relatively nothing about. I didn’t know the difference between cement and concrete back then. Obviously that’s the biggest joke going around now. But that practical application is so crucial in getting people even just excited about what’s on the other side. But then I think also making sure that they can make those connections between what they’re learning about when they come back versus what they’ve actually learned in their internship. But you mentioned something perfect, which was going to be my next question, is that in the classroom, are we starting to talk about the sustainability push?
Dr. Heather Brown:
I think we are. We actually have a committee within CIM that focuses on integrating sustainability in every course because it’s not just a standalone you talk about that sustainability piece for four hours in a 120 hour curriculum. You really have to re-approach sustainability from a couple of different directions. Where I think the gap is right now as I do think material producers are doing a good job of producing global warming potentials for their products, understanding EPD impacts, but there’s the handoff to the contractors that we have to understand a little bit more and what are they going to do with that concrete, with that asphalt, with that aggregate and how are they going to put it in place that is also less carbon intensive. So there’s a bigger picture still at play. I think we’re doing our part as material suppliers to try to give them the best low embodied material that we can. Are we there yet? No. But I think we’ve made a huge leap forward in showing the industry at large concrete in particular is a great material to lean on when you’re looking at long-term performance and then also that sustainability piece, both short-term and long-term.
Sarah McGuire:
Now, you also mentioned before that it’s really important that as we’re looking at optimization that we understand how all of these new materials, the new gradations, the combination of blending powders together and how those react so that we can create better mixes. As we further that knowledge on the optimization side, where do you think the responsibility lies to make sure that we’re furthering obviously yourself, but also the industry and bettering us as a whole?
Dr. Heather Brown:
That’s actually a really timely question. I’m having those conversations almost every day with my cement suppliers and my admixture suppliers because it’s a partnership. We have to link arms and be able to solve these problems together. And what I think has changed more than anything because of the introduction of these new materials is transparency and communication in a good way. What we understood before about cement or what admixtures could do, we have to now recreate basically new models of what admixture interaction and compatibility looks like with a newer type of cement. A 1L cement, for example. And then the cement companies have to understand that the test data they used to provide us isn’t telling us the whole story anymore because they’re doing different things to their cement production, which is changing the way it hydrates into our concrete mix. So while they’ve stuck with their classic test, it’s not giving us the information that we need.
So I have found that all three legs of the stool are having to get involved because we each have different testing capabilities. What I can do with concrete, they’re going to do with either cement or paste or mortar. And while that’s all very important, we have to be able to share that information so we can establish new trends. So we’re starting to actually have meetings specifically with cement and admixture suppliers and get in a room and talk about these things because we’ve got to be able to establish testing programs that help us predict what’s going to happen in the field, not be reactive to what’s happening in the field. We’ve spent the last two years being very reactive to all the problems that have surfaced due to material changes and availability, and none of us want to be in that. We don’t want to be on our heels. We want to be moving forward and providing solutions that we feel really good about, and contractors don’t have any basic concerns about what they’re getting on the other end because we have heard it from the contractors that things have changed for them too.
Sarah McGuire:
At the same time, you also said at the beginning of this that being reactive and the pace that you’re working at, there’s also a level of inevitability to that. So it’s interesting because hopefully that is where technology can bridge the gap. I’d love to understand from your perspective … IMI as I said, is certainly not the norm. You are leading the charge when it comes to adopting technology, looking at new practices. So I’m sure the optimization initiatives that you have within your organization are much more involved than what the industry is seeing at a whole. I’m curious to hear from your perspective what you think is the norm in the industry today around optimization goals, and then if you’re willing to elaborate on some of the things that IMI is doing that’s maybe a bit next level, I’d love to hear the comparison of the two.
Dr. Heather Brown:
Sure. So I think in general, we optimize until the point of we don’t hear customer complaints. That’s just the natural cadence of our work. Because obviously we don’t want to have our hair on fire every day so if we can get the mix to a point where we don’t get callbacks, then we just let it ride. You just say that, okay, the mix must be doing okay, we’re not hearing any customer complaints, and you just let that mix function without a lot of oversight. Now, if you have mixes that are constantly being used in your top 10 mixes, let’s say, then you’re getting data whether you want to or not because there’s just a lot of data to be had. But in general, optimization is only necessary if you’ve got problems. Now, we’re trying to think beyond that because there’s obviously a lot that we can do from a sustainability front, from an economical front, really from a standard deviation and coefficient of variation front. We want to make our mixes more repeatable. We don’t want to have drift in our standard deviation or massive over design or gosh, a mix can even drift to the point where we have minimal over design and we didn’t catch it. So we’re trying to make sure we’re just more consistent. And I think that has started really showing itself in our boots on the ground.
So we have a really good team of quality control professionals who are making samples, running tests, doing cement baseline testing, really getting out there and talking to the customer. Without that, I don’t know that we would know when to optimize. I think we would be too late. We would have more problems than we would want because we weren’t really listening to the feedback. So getting that proactive feedback allows us to go back to the drawing board and tweak things. A big one right now is water demand. A lot of these powders as they get blended, just need more water. Well, that goes against everything that we do in a mix design because we’re always trying to minimize water, lower the water-cement ratio, and that’s been a big battle because truly the mix needs more water. It’s not chemicals that it needs, it really needs water. And so there’s a balance in what admixtures can do and how it can help solve our problems and what truly just basic good water demand, how can it be addressed in a way that engineers aren’t going to throw their hands up and basically deny your mix because now you’ve had to go up 0.1 or 0.01 or 0.02 in your water-cement ratio.
So those conversations are starting to happen, which is good. It’s just definitely going against the basic mixed design methodology that we all have become very comfortable with and then what you see in a basic concrete specification. So that’s a big change now, but I think people are receptive and open to the idea of new concrete’s going to need a new mindset.
Sarah McGuire:
You’re going about these practices for very proactive reasons, which is really neat to hear, and I want to dive into some of the things that you specified before. But overarchingly, it’s very customer driven at the end of the day. Everything’s about the customer. Making sure that they’re happy. And unless a customer says otherwise, most companies that are just trying to stay on their feet every day, they’re just going to go about their day to day and not worry because like you said, no fire, no problem. So if you were going to a company that was much, much smaller, a company that’s not experiencing a lot of customer issues, but definitely has a lot of over design, definitely has a lot of room to improve, what would you say to convince them that this is worth looking into and carving out time?
Dr. Heather Brown:
Well, in general, optimization can help you rein in some costs. What I think we have gotten trapped into though is over design does help you mitigate the risk of all the people touching your concrete. That starts with the driver. We lean on our drivers. Our drivers are our most important part of our workforce to deliver to the customer and to be the face for the company, but they also have a certain responsibility in serving that customer. And some drivers take it upon themselves to “get the mix ready” for the customer because they know what the customer likes. And while that sounds wonderful, it does mean that your mix that you’ve spent so much time optimizing and adjusting and trimming, they’ve now just taken it into their own hands and put something to it. Water is usually the most common thing, or maybe they’ve decided to rev up the drum and mix it a certain way and that might change the air content. There’s all sorts of things that driver can do to impact that mix that we have very little control over. And it’s all really in good form because they’re trying to get it ready for the contractor, but the contractor doesn’t know some of those things have happened and then they add their layer of influence onto that mix as well.
So I do think that with smaller companies, I think that they don’t always have the ability to control all of those things, but large companies don’t always either. So I think we’re all held victim to the impact that all of these different stages of the life of a concrete mix has and how the impacts of a driver, a finisher, testing lab can have on the final product. And that keeps us all up at night. That’s the one thing that we all try to fix in our companies. But what I would tell a small company is if you’re trying to optimize, you want to create something that is very consistent and the drift and mixes is what really hurts everybody. Once you start drifting and adjusting too much and really trying to be too responsive to a contractor and you change a mix too much, then now you don’t really know what’s going out the door ever because you’re always trying to change and adjust and shift. And small companies may be more nimble and be able to do that a little bit easier, but then now they have 16 different iterations of a mix that should be able to go out the door with very little change depending upon the seasons of course.
Sarah McGuire:
It’s very interesting on the driver’s side because obviously they are the most important part of this business. And I think the companies that are doing the best out there recognize that. We are working with a company … I won’t name them by name. But one of their biggest mandates has been over the last couple of years, they’ve spent a lot of time making it so that their drivers are drivers, not concrete truck drivers. That they don’t need to know the ins and the outs because they’re looking forward and they’re thinking, how hard is it going to be to continue training people to see a slump test done and just go, oh, that’s a three-inch, oh, that’s a four-inch, or, oh, that needs water, I know what happens here. And to just have that innate knowledge to be able to make those tweaks.
They were looking at it knowing that this is going to be a huge gap in the labor market moving forward, and they’ve spent a lot of time trying to make it so that their drivers don’t need to be concrete experts. That you could find someone who is a … My father was a transport truck driver for 30 some years. They want it so that someone like him could just jump into a truck tomorrow and with a little bit of training be up and running. But I know that it’s a bit controversial and I’m wondering what your thoughts on the future is. I don’t think we’re anywhere near that now, but if you heard that or you were speaking to maybe the owner of this company that’s trying to work towards that, what would your thoughts be with them?
Dr. Heather Brown:
I like that train of thought. I think there’s a balance. We just the other day had a driver call in and start telling our QC manager some of the things that they were seeing on the job, and that doesn’t happen that they would take the time to call a QC manager. Typically, they’ll call back to the plant or they might just process it in their own head, oh, this time the slump wasn’t that great, so next time I’m going to show up one inch higher. And so they’ll process that internally, make those adjustments, and we never know what’s going on. But when that driver actually called a QC manager and said, “Hey, I’m seeing this on the job. What do you think?”, a light bulb went off for me, and I thought, that’s the communication that we need. We don’t need them to worry and make the adjustments and think it’s all on them. Put that on us because our job, that’s not their job.
So to your point, can we take some of that pressure off of them to feel like they have to be responsive and be alert enough to understand concrete enough to make proper adjustments? No. I don’t think that’s fair to train somebody to be a good driver and then turn around and hand them this technical firebomb that could go off any day and make them responsible for that at the end of the chute. I think that is why we’re in the quality control position. So I remember talking to the QC manager thinking, we need to highlight this. This needs to be somehow bottled up and figured out how do we create a communication link between a driver and the QC team. Now, if a QC professional is out there alongside the truck because they’re taking cylinders, those conversations are happening organically and that QC person’s able to jump on their computer, remote into the plant and make adjustments right there. So that’s great. We can do that, but we’re not at every job. We’ve got lots of yards of concrete going out every day, and we’re maybe … I ran a number one day. We’re probably at about 5% of our yards going out every day, so we’re only eyes on 5%. So that other 95%, that’s on the driver, and that’s a big task.
There’s no amount of onboarding and training and repeating ourselves and getting on our soap boxes that’s going to allow them to truly embrace what we need them to do. So I agree. I think the future is finding a different communication link that they can … If it’s on their tablet or if it’s a radio or a phone or something, a touch screen, “Hey, I’m seeing this at the field. I think adjustments need to be made.” A simple touch of the button and now we can turn around and make these remote adjustments on the fly.
Sarah McGuire:
Heather, that’s so interesting because a lot of what you’re talking about with these drivers is they are communicating these things. They are making these tweaks. But if they’re not communicating it directly with you or they’re not recording it somewhere, where does that data go? And then how do you optimize later? Because you actually don’t know what was batched, what was delivered, what was tested, and therefore optimization is so limited. And that’s been a huge issue that we’ve run into is just because we have these algorithms that are producing amazing results, getting the data has been such a challenge. Not just acquiring it in an efficient way, but then also it’s just not there. How are we supposed to produce concrete that is pumpable and workable when we’re not really gathering data that would solidly explain that when we bring new employees? And I’ve started showing them how is a slump test done? And then I explain to them how many trucks go out onto a job and where does that data go?
There’s this one YouTube video that we show all the time, and I say, they’re doing this perfectly right now. This is not how it’s done. This is not normally how it’s done. Sometimes it’s not even done. We can be honest about that. So when we’re talking about the data that goes into optimization and how we get that even with a team of your size with all of these experts that we’ve been so lucky to work with, I’m curious to know what are the biggest data challenges that you see even as a company that’s adopted all of these practices?
Dr. Heather Brown:
It’s exactly what you just said. It’s all of the backend performance features that we don’t have data points to then circle back to the actual mix and say what we did in the mix is working in the field. And we would need to do that not only for the mix itself and for the conditions that it’s in, but think of all the adverse conditions our concrete is put in. So we’re taking that concrete and we’re making that same mix, create good product at 95 degrees and then we’re turning around and trying to pour it at 28 degrees or a windy day or a frozen subgrade.
We’re trying to take concrete, a basic mix and subject it to all of these conditions. So I really do believe that there’s work to be done and AI is going to help be able to gather this information. Now that’s going to turn our quality control professionals and our drivers into almost like interviewers on the job. We’re going to have to be asking the right questions. We’re going to have a whole new slate of questions to be able to understand do you need to rate this pump ability, rate this finish ability. Let’s get that information back into the queue and that allows us to understand, did what we optimized just work in the field? It’s not enough to look at strength and to look at set time to really understand what’s happening in the field. So I agree that the data is almost daunting on what we’re going to have to acquire to be able to make those adjustments. But I think it is the next step our industry has to go and technology is going to get us there.
Sarah McGuire:
Right. Now we’re talking a little bit about testing of strength. Obviously we’re a company that we’ve made sensors that go into the concrete that are supposed to give you a little bit quicker and also being cloud-based, it helps consume that. But of course, we’re not naive to think that everyone’s just going to start using sensors tomorrow and we’re all going to use that as the source of truth. So when it comes to optimization, something I’ve always said is you really can only optimize as far as your testing will allow you. And your testing that you have on every job is so subjective to the players, the requirements that are on the job, on the specifications … How often do they even need to do the testing and that might not match what you need to then get the feedback that you need back on your concrete. So AI and optimization and all of that has a long way to go, but what do you think are some things that people could be doing now to prepare for the inevitability of being able to use that?
Dr. Heather Brown:
We just need more of the data available. I think we’ve got to convince architects and engineers that just having the data set, whether it is knowledge that you need on that project or not, it’s helping to build trends that we don’t have in lab-crete. We can pull cylinders and we can make sets in the lab and show them what 73 degree concrete should do. And that is the standard. That’s what we as producers are held to is essentially the lab strength of field-made cylinders. We take them back to the lab, we take care of them, we put them in the bath, and we get pushback on that because they’re like, well, that’s not real world. Well, that’s not what the standard is. So if we’re going to ever get to the point where we’re talking about what the concrete’s doing in the field … We do the field cured cylinders, we get that. But again, that’s a minimal data set.
If we had data on every mix of concrete that was going out in every condition, whether we needed that for one day PT or three-day traffic opening or not, then we could start building trends of field concrete and understand even more what’s going to happen in these wide range of temperatures that we’re subjected to and wide range of humidities. We’d actually know how to respond and we don’t now because we’re taking care of the concrete in the way that ACI and ASTM specifies so that we’re paid for that performance. And right now that’s the safety net that we’re going to lean on. But until we have more data in the field, I would not want to subject a producer to the risk of a contractor changing the properties of that concrete and then we’re held to the standard of that concrete in place. I think we’ll get there. I would like to get there, but it’s going to take a lot of data and I don’t think you could do that without sensors.
Sarah McGuire:
Yeah. That’s a good point. And I think there’s lab and then there’s field, and then there are sensors because typically when we’ve done the comparisons of our sensors to the cylinders, if anyone has never used maturity sensors are in-place sensors before we tell you right away, you are not going to get comparable results against your lab. The closest you’ll get is a field. And we usually ask them to put a sensor actually in one of those field cylinders just so that they can actually see something that is going to be accurate because it shouldn’t be. One should be much, much higher than the other in terms of how quickly it’s curing. Let’s say hypothetically you were doing a concrete pour and the field cured were coming back over and over very, very high, and it gave you the internal confidence to say, we could absolutely reduce cement or change some components of this concrete to move forward, but your lab just simply didn’t allow for that, or at least maybe the third party lab didn’t allow for that. What would you do in that scenario? Would you even give it a go or at present you would just say, forget it’s not worth arguing about?
Dr. Heather Brown:
Well, we do make a lot of companion sets for that very reason. And sometimes we do make the choice of leaving some in the field to prove that point. We can take our cylinders back to our own lab, break them and show them that we’re fine. But can we show you that when properly cured and treated, even though they’re in the field, can we show you that the strength development is similar or at least trending in the right direction or potentially way above what you actually needed? One of the games that we have to play with engineers is they’re so hung up on the water cement ratio that we end up having to go up in strength to meet that. Even though we don’t need that extra 500 or a thousand PSI, we are doing it simply because they have a real rigidity towards increasing the water cement ratio for that particular application.
So sometimes taking the time to make those extra cylinders to show them, look how much you just over designed. And we’re in the field here, so we just want to use that information as collateral for the next project. And we can sometimes convince an engineer once we show them a body of work to say, okay, we had four projects where we did this and you really don’t need that much over design. Our concrete can handle what you’re needing at a 0.47 versus a 0.45. And so we do try to take the time to use both lab and field data and sensor data to build an argument to change the mindset. And the only other way we think we can do that is if we can include some performance testing like shrinkage or freestyle or permeability to further reinforce it’s not just about strength. You’re actually needing these other performance factors and we’re meeting those as well. So we want to make sure the engineers feel comfortable about it. So we’re always going back to the spec with them and saying, here’s an opportunity for us to open the conversation up and here’s some data to support that. But it is hard to get enough physical manpower to build that data set on our projects.
Sarah McGuire:
Yeah. And that is a really good segue into some of the questions I had for you on working with prescriptive requirements. In Canada it’s almost a completely performance-based market, but obviously it’s not like that across the United States, and it varies from projects, state, municipality, everything like that. It’s all over the board. Have you seen real changes in the last 20 some years of people’s reliance on prescriptive requirements, or do you see sometimes a shift that’s happening or you only see it on a one-off basis? Because I think those one-off cases are promising, but if they’re one-off and it continues to be one-off over and over, then we’re not really seeing real change there. And I’m wondering if you see a future in which it will be almost entirely subjected to the producer to say you’ve earned the right to do whatever you want.
Dr. Heather Brown:
That’s a great question because I think it’s a roller coaster. I’ve been around long enough to see performance be spotlighted and highlighted to where I really thought true change was occurring. And then I feel like we take 10 steps back sometimes, and we face some engineers that are still stuck in the 80s and stuck in the 90s and still want to just lean on what they’ve always done that’s not changing. But then their mentors to the young engineers. And so unfortunately, the young engineers get caught up in maybe their company’s practices and it’s sometimes even difficult to approach a young engineer. So I don’t think performance is where it should be. I do think that sustainability may help us get there. And the reason I think that is because when you look at a sustainability specification now it’s all about SEM replacement or cement replacement. That’s the big lever that they want you to pull is can you take out 50, 60, 70%?
Well, that then talks about real performance. Are we going to be able to set in the timeframe that you want to set? Are we going to be able to build the strength in the timeframe that you need it to be? Are we going to be able to still resist cracking and shrinkage and whatnot? So it has opened up a conversation because sustainability opened the conversation and now we’re talking about performance. And so then water cement ratio seems like such a tiny thing and the whole scope of the job because we’re addressing such a much bigger purpose of that mix now. And so strength being a big one as well. That’s one that can hold things back. Well, let me show you what the strength’s going to be with all of this replacement. Now I’m going to need a 56-day requirement, possibly even a 90-day requirement to hit your sustainability goals. Completely changes the conversation on what true performance looks like in a mix and how different applications truly do need different things.
And not that engineers didn’t realize that before, but it just allows us to be that much more custom and we’re coming to the table with solutions that they really need because they’re trying to hit other targets like sustainability and potentially even life cycle costs. So I think that’s helped us. I just don’t think it’s been sweeping, and I don’t think it’s been adopted wholesale. I actually presented to a couple of engineers not that long ago, and they rolled their eyes nearly the entire presentation. They were not into anything I had to say about sustainability or about performance or about water cement ratio adjusting. It was all snake oil to them.
Sarah McGuire:
Well, what did they come to the table for?
Dr. Heather Brown:
I asked the same question.
Sarah McGuire:
I certainly don’t have the knowledge in the field or in the academic setting in the same way that you do, but I certainly relate to the walking into a room and people looking at you going, “What on earth are you going to teach me that I don’t already know about concrete?” I definitely have gotten that a lot. But you’re describing a really interesting chicken and egg situation. I think the sustainability push eventually is going to be mandated to a certain degree, but how quickly that takes off is still very much up for debate. I think we’ve talked about this for years, but what stakeholders need to come together to actually create real change, because we can go on these seminars and we can do these talks all we want, but there has to be a call to action.
Dr. Heather Brown:
I think there’s a lot of different people that have to get involved. I think it’s almost too late if you wait till you’ve got a seasoned engineer and you’re trying to convince them that we need to do things differently. So I do see trade associations playing a bigger role in creating curriculum. And I have seen organizations like PCI, the precast industry, they’ve done a great job of actually creating learning outcomes and learning modules, and they’re sending it to students and to college professors for free to say, please teach this because this is what’s really happening. We want to make sure that your students are prepared to be able to design a bridge beam in the right way to support an actual bridge with actual traffic. And it’s not just out of a textbook. We’re going to include all the nuances, all the things that affect how to build a good bridge beam that don’t show up in a textbook. And I think all trade associations should get behind some level of curriculum.
Sarah McGuire:
And on one hand as well, I think a common complaint about the younger generation coming in is that they’re not thinking with a practicality hat. They’re coming in and they’re bulldozing. They’re saying, why are things like this? And they want to demand change immediately. So there’s that aspect that we can prepare them for how to enact change. But then there’s also the side of our industry where companies like yourself and our associations at NRMCA where we can also prepare ourselves to be willing to listen and be open-minded and put the right protocols in place to once something is suggested, okay, how do we actually move this forward? But I think all of this does segue back into AI because as we’ve said, it’s very reactive of an industry that we’re working in. So as soon as we want to bring change into the industry, there’s a process that needs to be followed to make sure that it’s done safely.
And to do that, we need time. And time is just certainly not something that we have a lot of in this industry because it’s go, go, go. So how do we allow for more time to be able to drive things forward? And I think that’s where AI can make a huge, huge play, not just in optimization but everywhere. I’m curious, as somebody who is already looking at different solutions like this, you’ve adopted a lot of technology even outside of AI, but ones that will enable the data that will be eventually needed. What factors should professionals keep in mind as they incorporate AI into their business? Or at least start investigating it to decide if it’s right for them and when it’s right.
Dr. Heather Brown:
I do think how data is captured and analyzed can be daunting and a little bit scary. So IMI has taken the approach of hiring a couple of computer science professionals to work within our organization, and that has made a huge difference. Because how they look at data is very different and how they process it and how they get to it. They seem to have the ability to backdoor an scrape data in a way that gives us more information than we knew we had. Because there’s so many dashboards from different tools and technologies that show us the best of the best pieces of the data. But if you really go behind the scenes and pull the curtain back and you start really pulling all of that raw data and processing it, we can make adjustments that we didn’t even realize we could make.
Sarah McGuire:
Yeah. I think so much of what we talked about today has really led to the importance of having all of that data in one place. The consolidation of bringing all that communication together. The more that we can learn that. And looking at IT as more than just help, my computers not working and really looking at it like a solutions landscape and how we can bring all that together, I think makes a huge difference. Coincidentally, the next episode that we’re going to have is we have an IT professional from the industry that’s going to be coming on here and talking all about that and the importance of cybersecurity as we bring all of that together and really making sure that we’re putting the right protocols in place.
Dr. Heather Brown:
That’s right.
Sarah McGuire:
Well, thank you Heather, so much for joining us today. We really appreciate all of your time and your expertise. Yeah. I want to say thank you so much.
Dr. Heather Brown:
I enjoyed the conversation. Thank you, Sarah.
Other Related Episodes
Episode 46 |
July 11, 2024
The Optimization Journey Has Just Begun
In the eighth and final episode of our "Building Better with AI" mini-series, "The Optimization Journey Has Just Begun," we’re introducing a unique twist. This time, Sarah McGuire, AVP Business Development, switches roles and steps into the hot seat to answer questions rather than ask them. To guide this special conversation, we’ve brought back our Co-Founder and CTO of Giatec, Aali Alizadeh, Ph.D. This episode provides a comprehensive update on where SmartMix, Giatec’s AI-powered mix management system, currently stands. Sarah and Aali discuss the significant progress made since recording the first episode in December 2023, highlighting the challenges overcome and valuable lessons learned during the implementation of SmartMix. Listeners will gain insight into customer success stories and the transformative impact SmartMix has had on the concrete industry. This episode offers a reflective and forward-looking perspective on the journey of SmartMix, showcasing how it continues to drive innovation and efficiency. Tune in for a compelling discussion that not only recaps our journey but also looks ahead to the future of AI in the concrete industry. Don’t miss this insightful and engaging conclusion to our mini-series!
PLAY
Episode 45 |
June 27, 2024
The Daily Life of a QC Professional
In the seventh episode of the "Building Better with AI" mini-series, host Sarah McGuire explores "The Daily Life of a QC Professional" with Bryan Fulcher, VP of Technical Sales and Services, Maschmeyer Concrete. Drawing on extensive industry expertise, Bryan provides a glimpse into the multifaceted role of quality control professionals in the concrete sector. The conversation begins with Bryan's career journey and the evolving expectations and challenges faced in QC over the past two decades. Throughout the episode, Sarah and Bryan delve into key topics such as misconceptions about QC, the integration of AI and technology in enhancing efficiency, and preparing for the future of AI-driven QC processes. Bryan shares practical insights into managing daily operations, handling technical challenges, and fostering industry-wide innovation. Tune in now to gain a deeper understanding of the pivotal role QC professionals play in shaping construction standards and driving quality assurance in the concrete industry!
PLAY
Episode 44 |
June 13, 2024
The Future of EPDs in Concrete
In the sixth episode of the "Building Better with AI" mini-series, host Sarah McGuire delves into “The Future of EPDs in Concrete” with featured guest Juan Gonzalez, Manager of Strategic Development & Sustainability, Vulcan Materials. With a wealth of experience, Juan shares valuable insights into his journey within the field of sustainable construction and environmental practices. The conversation begins with an exploration of the history and evolution of Environmental Product Declaration (EPD) reporting, highlighting Vulcan Materials' pioneering efforts as the first company to produce EPDs with Climate Earth. Throughout the discussion, Sarah and Juan address questions surrounding the role of EPDs in modern construction. Juan elaborates on the motivations behind Vulcan Materials' early adoption of EPD reporting, the challenges faced in championing this initiative, and the regulatory standards that have been influential in driving EPD adoption further. Tune in now to gain valuable insights that could reshape your perspective on EPD reporting and drive meaningful change in the industry!
PLAY
Want to Be a Guest Speaker, Sponsor, or Just Have a Question for Us? Fill In the Form!