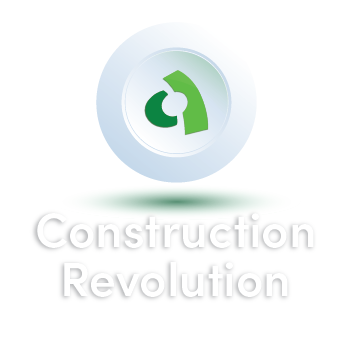
Episode 20 |
September 16, 2022
Bringing Lean Principles to the Construction Industry
In This Episode
In this episode of the Construction Revolution podcast, we sit down with Jonathan Harvey, Founder and Principal of The New Jobsite. Jonathan founded the company in 2019, after over 15 years on jobsites where he was constantly thinking of ways to build faster and safer, with better tools and less waste. He explains how the company helps contractors by deploying on-site productivity solutions using the 5S lean principles. Join us as he discusses trends and innovations in concrete and the broader construction industry. Learn how The New Jobsite’s Tool Management System can help you implement lean construction principles on your jobsites to make your workers happier and more productive.
Host
Andrew Fahim
Director, Research & Development, Giatec Scientific Inc.
Guest
Jonathan Harvey
Founder and Principal, The New Jobsite
Podcast Transcript
Andrew Fahim:
Hello, there. Welcome to the Construction Revolution Podcast. My name is Andrew Fahim. Here, in the show, we explore the latest trends, technologies, people, and organizations that are revolutionizing, or disrupting, the construction industry. They’re changing what the industry would look like tomorrow. Today, on the show, I’m speaking with Jonathan Harvey, the founder and CEO of The New Jobsite. Jonathan has spent the past 15 years on job sites where he was constantly thinking of ways to build faster and safer, with better tools, and less ways. As a result, Jonathan founded The New Jobsite in 2019 with the goal of enhancing the industry’s ability to build beautiful, solid, and sustainable structures by improving the way that the structures are built, to allow everyone to live, work, and travel in beautiful, plentiful, and sustainable build environment. The company currently offers a tool storage system, which was designed using lean construction principles that allow contractors to achieve a clean, safe, and organized job site. In addition, they offer consulting and training on lean construction principles.
All right, Jonathan. Thank you so much for taking the time to chat with us, today. I’m very excited to learn a lot more about you. Then, about The New Jobsite. Just to kick things off, can you tell us a little bit more about The New Jobsite, and maybe, what led you to start the company?
Jonathan Harvey:
Sure, Andrew. My pleasure to be here with you. Yeah. The New Jobsite is a fairly new company. I started it three years ago. I’ve got a background in construction and business. I was working for a large GC in Western Canada. I thought that there was lots of issue that need to be addressed in the organization of tools and productivity solutions that the company could use to improve itself. I started The New Jobsite to address those issues.
Andrew Fahim:
Awesome. I read about The New Jobsite a little bit, and it said that it focused on increasing construction productivity by implementing things like lean construction. Can you tell our listeners a little bit more about what lean construction is, and what it tries to address?
Jonathan Harvey:
Yes. Actually, we’ve got a pretty wide spectrum that we focus on, but our main aspect is on-site productivity solution. We work with general contractor mostly, and we help them improve their productivity. By lean construction, I mean we use a lot of tools that Toyota put in place back in the early 1980s and 1990s, but haven’t been implemented in a construction company. We work with a general contractor that is specialized in concrete. We go off that. Then, we take a listing of all their tools, every consumable tools and safety supplies that they use. Then, organize a trailer, or tool storage solution, for them, to help them improve the productivity and improve the safety of their worker.
Andrew Fahim:
Oh, it’s very interesting. Okay. What kind of benefits does a general contractor get out of this? Can you tell us a little bit more, maybe, some of the numbers that they get? What disadvantages are there, as well?
Jonathan Harvey:
Yeah. There’s many, many benefits. They’re kind of hard to quantify because you get the productivity benefits from the worker, first. Actually, when I was working with that general contractor, back in the days, every day we lose an hour, two hours sometime, looking for the right tools. We had guys leaving the job site and going to the tool crib, or the store to buy tools that they were missing. When you have everything on-site, everything in your view, you can save an hour, an hour and a half, per worker every day. Usually, on the productivity side, you save 10, 15% more time on the productive front with the use of our tool storage system. It’s much more positive for the worker, too.
Because you work in a more organized and cleaner environment, you’re happier. You don’t get mad because you cannot find the right tool at the right moment. You just go in the trailer, or in the C-CAN, and then you find the right tools. What happened when you go in the trailer, and then you cannot find something, you get mad. You get kick off your plan. You have to leave something. Then, your teammate that’s on the job front, is waiting for you. While he’s doing that, is not doing his job. Also, there’s a benefit, too, on the cost saving for contractor. First, you find the tools this year, and then you know where they are. You don’t go buy stuff that you don’t need when you can see that everything is there at the job front for you to use.
Andrew Fahim:
Jonathan, in a collaborative environment like a job site, where we have so many different stakeholders using so many different tools, do you typically see this system still working when two different people that [inaudible 00:05:50] each other are starting to use the exact same tools? How does this storage environment still work in such a messy environment?
Jonathan Harvey:
Yeah. It can get a little more complicated. Usually, subs, they each have their own tools. General contractor have their own tools, too, that they don’t really share. A construction can get messy, sometimes. People lose stuff. They like to work in a cleaner and more organized work phase. By having their toolbox and their C-Cans more organized, makes everyone happier. Yeah. It can be difficult to get the workers to bring the tools back where they are, and use the system to its full extent.
Andrew Fahim:
That’s very cool. Okay. Jonathan, I’ve been reading about this whole 5S concept. Maybe, tell me a little bit more about those five Ss. How do you guys use this to basically lean tool, or something that would help on job sites?
Jonathan Harvey:
Mm-hmm. Yeah. 5S, Toyota invented that system. Basically, 5S stand for sort, set in order, shine, standardize, and sustain. The first step is actually to sort the tools. You get rid of everything that you don’t need. You just keep everything that you need to do that particular job. You organize them by the way… The tools that use the most often has to be the more accessible and closer to where you need them. The tools that you don’t need, you put them lower. Basically, build a big shadow board, it’s called, to organize the tools.
You sort, then, you set in order. Like I said, you prioritize by the amount of time you use each tools. Then, you shine. By having all the tools in your face, helps you clean the tools, and fix them to make sure everything works properly when the next tradesmen come and want to use that tool. You shine. You clean your tools. You make sure everything is functioning properly.
Then, you standardize. It can be color coding. A large company, usually they have multiple units that will do production so they can have five, 10 trailers. If you go from one trailer to another, you don’t want to change the whole setup of the tools. You want to make sure everything kind of stay in the same place. Say, if you switch your workers from one job to another, they walk into the other trailer, and the drills are exactly in the same spot on the left. Then, you can color code, too. Can be a little bit of paint, or tape, or whatever, so you can have all the piercing tools in one color, and all the concrete tools in different color, and the wood tools in different color, and on and on. You get the basic principle.
Then, sustain. It’s actually to keep going at all that organization, and all that cleaning. It’s one thing to have the setup and have everything in place, but the workers have put the tools back in their place. Then it’s just useless, if you have a bunch of rack on the wall, and all the tools are sitting on top of a desk, and just piling up. It’s not going to be any faster. You are just going to make sure your workers put the things back in place. You give them prize, or little incentive, to make sure that they follow on with that principle.
Andrew Fahim:
Love it, love it. It’s really the sustained part that’s, perhaps, the most challenging. Yeah. For me, here, we run labs where we set up very nice systems. If you cannot sustain these systems for a long term, that’s probably, in my opinion, the most challenging part. I don’t know if you agree, or not.
Jonathan Harvey:
Yes. I certainly agree, Andrew. The workers, sometime they get used to habit. At the end of the day they get tired, and they just want to go home. They don’t don’t want to spend 15 minutes, at the end of the day, organizing and cleaning your tools. The next day, that’s when you’re happy you’ve done it. You show up to a nice, clean worksite. You find what you need, and that’s the most important.
Andrew Fahim:
Yeah. Absolutely. Jonathan, I also know that you’re very involved on the training side of things. Maybe, tell us a little bit about the gaps that you see in today’s construction, or in today’s skill set for construction. What do you think is the main things that we really need a lot more training on?
Jonathan Harvey:
Well, construction’s going to be more and more technological. We need to teach the trade. In the first place, how to use computer, too. We need to let them know that construction is more technological. They need to be able to use computer, use robot. It has to be a part of their job, to make their job more diverse by getting them to actually use those tools that make them more productive. Technology mixed with trades, I think it’s a very bright future for future trades people.
Andrew Fahim:
Right, right, right. Okay. Since you also have a lot of experience on the consulting and training side, maybe when it comes to concrete… Maybe, I’ll start there, and then we can get to tools. What new applications and improvements have you already seen, and what do you think the future holds for the concrete construction?
Jonathan Harvey:
Mm-hmm. Concrete is a very interesting industry, as you know. You’ve been working with concrete for a long period of time. Yeah. I think that’s one of the material of the future. Right now, I’m working with a contractor, too. We’ve been doing a lot of work with the insulated concrete form, which is fairly recent in Canada. It’s been around for 15 years, about. It makes work much more productive. Also, advancement in the concrete production technology. It’s a big thing to make the concrete more environmentally sustainable, greener. There’s lots of new material coming that will be replacing the cement in some ways, and lots of interesting research, and all those kind of way. With concrete, you can basically build any form so it’s very hard to replicate. You just need to improve the way you build a mold, and basically you can build anything. 3D printing, obviously, I’m sure lots of your listener have been-
Andrew Fahim:
Yeah.
Jonathan Harvey:
… hearing about the 3D printing technology. It’s getting more and more present on construction site. I think there’s a new company in Ontario that started building houses using 3D printing technology. I was actually at World of Concrete in February, this year. One of the big attraction of the show was Cobalt International. I’m sure you know about it. They’ve sold, I think, between 50 and 100 printers, now. They’re building house all over. That’s something that’s getting to a worksite near you. We still haven’t used it with our customers on-site, but I’m sure there’s going to be lots of application coming out of that.
Andrew Fahim:
Interesting. Yeah. I know 3D printing does come a lot when we talked to a lot of our guests, here, on the podcast. Do you think something, like 3D printing for instance, can help with lean construction? Do you think that would advance it, or do you think that this is more of a hindrance to it?
Jonathan Harvey:
Yeah. At this point, there’s advantage and disadvantage to this method. I’ve seen people using it successfully to build components for building. If you want to build components that are way more intricate, or forms, basically, you don’t have the mold limitation that you have with traditional concrete. If you want to build a curved wall with traditional concrete forming, you need very skilled carpenter to build that mold. With 3D printing, you just program the computer, and it’s just going to do it for you, perfectly, the first time.
Andrew Fahim:
I guess it’s lean by definition, in that sense. Jonathan, you’re obviously very excited about the newest technologies that are coming to job sites. Maybe, tell us on the tooling, or the machines, or the technology side, what kind of things are you most excited about? What do you think will change the way that we work on job sites?
Jonathan Harvey:
Yeah. It’s a lot of work to change the way that we building. Construction’s been around for a long time, and the material has been built for a long time, too. There’s huge mills that throw a bunch of 2×4 and sheets of plywood out, every day. Those things need to be used. The robots, that’s one thing I’m very interested about. Single-task robot are something that are getting more used and used on the job site, nowadays. You can see that Hilti is getting into the field. They have a Jaibot, that’s a drilling robot. People use it for the ceiling. Okay. I don’t want to throw too many company’s name around, but there’s robots for excavator, too, that can help contractor to replace operators. We got a big problem, partially in Canada, getting skilled tradesmen to work. Everything that can help reduce the load that those tradesmen need to do every day will be very good for us.
Andrew Fahim:
Absolutely. Jonathan, tell me a little bit about what’s next for you guys. What are you, maybe, working on? Tell me what’s under the hood.
Jonathan Harvey:
Yes. We’ve got lots of projects. Basically, we’ll work with our customers to see what’s the most beneficial for them. Obviously, we’re constantly improving our tool storage system. There’s lots of new tools coming, and there’s always new holders to design and produce. Also, we want to test some products, and go more into the robotic side. That’s something that we’re looking for the future.
Andrew Fahim:
Okay. That’s awesome. Okay. Jonathan, when you see, maybe, construction in, let’s say 10, 15, or 20 years, what do you see as the biggest change that’s going to happen for this industry?
Jonathan Harvey:
I think the biggest change going to be a lot less manual installation. Materials use on the site have to be improved to make it more suitable for robot to install those materials. People just don’t want to do the robot, anymore, and install 100 sheet of the gypsums every day. We can use robot for that much more efficiently. Just need to improve that. I think there’s going to be still lots of human on job site. They’re going to be a co-working with robots, and all kind of artificial creature, that will help them do their work.
Andrew Fahim:
That’ll be amazing. Okay. That’s a future that I’m very excited about, as well. That’s amazing. Well, Jonathan, appreciate your time. Thanks for taking the time to chat with us, today. It was really useful for us to learn a little bit more about your background, and your company’s background, as well, and all the cool stuff, and exciting stuff, that’s happening in construction. I’m very excited, actually, to have a two-storage system within my lab. I think that would be very beneficial to myself, and everyone that works with me. Jonathan, I appreciate it. Very excited about your future, and the stuff that you guys are doing. Hopefully, we’ll remain in touch.
Jonathan Harvey:
Sounds good, Andrew. My pleasure talking with you. Just stay in touch. We can that organize for you.
Andrew Fahim:
Awesome. Thanks so much, Jonathan. Have a good day.
Jonathan Harvey:
My pleasure. Bye.
Other Related Episodes
Episode 46 |
July 11, 2024
The Optimization Journey Has Just Begun
In the eighth and final episode of our "Building Better with AI" mini-series, "The Optimization Journey Has Just Begun," we’re introducing a unique twist. This time, Sarah McGuire, AVP Business Development, switches roles and steps into the hot seat to answer questions rather than ask them. To guide this special conversation, we’ve brought back our Co-Founder and CTO of Giatec, Aali Alizadeh, Ph.D. This episode provides a comprehensive update on where SmartMix, Giatec’s AI-powered mix management system, currently stands. Sarah and Aali discuss the significant progress made since recording the first episode in December 2023, highlighting the challenges overcome and valuable lessons learned during the implementation of SmartMix. Listeners will gain insight into customer success stories and the transformative impact SmartMix has had on the concrete industry. This episode offers a reflective and forward-looking perspective on the journey of SmartMix, showcasing how it continues to drive innovation and efficiency. Tune in for a compelling discussion that not only recaps our journey but also looks ahead to the future of AI in the concrete industry. Don’t miss this insightful and engaging conclusion to our mini-series!
PLAY
Episode 45 |
June 27, 2024
The Daily Life of a QC Professional
In the seventh episode of the "Building Better with AI" mini-series, host Sarah McGuire explores "The Daily Life of a QC Professional" with Bryan Fulcher, VP of Technical Sales and Services, Maschmeyer Concrete. Drawing on extensive industry expertise, Bryan provides a glimpse into the multifaceted role of quality control professionals in the concrete sector. The conversation begins with Bryan's career journey and the evolving expectations and challenges faced in QC over the past two decades. Throughout the episode, Sarah and Bryan delve into key topics such as misconceptions about QC, the integration of AI and technology in enhancing efficiency, and preparing for the future of AI-driven QC processes. Bryan shares practical insights into managing daily operations, handling technical challenges, and fostering industry-wide innovation. Tune in now to gain a deeper understanding of the pivotal role QC professionals play in shaping construction standards and driving quality assurance in the concrete industry!
PLAY
Episode 42 |
May 16, 2024
In this episode of The Construction Revolution Podcast, we are joined by Aviv Leibovici, CPO & Co-Founder of Buildots. Aviv brings a mix of technological innovation, and visionary entrepreneurship to the construction industry. Join host Steven Rossi as he delves into Aviv's remarkable journey from an esteemed educational background in computer science to the groundbreaking establishment of Buildots. Discover how Aviv and his team are revolutionizing the construction world with AI-driven technology that transforms construction sites into digitized environments for real-time tracking and decision-making. This episode offers a deep dive into how Buildots' platform is influencing major construction projects worldwide, enhancing efficiency, and redefining traditional construction methodologies. Don't miss this episode to learn about the fusion of AI, computer vision, and construction management through the lens of Aviv Leibovici's unique experience and vision. This conversation is a treasure trove of insights for anyone fascinated by the intersection of technology and construction, and it underscores why Aviv's leadership at Buildots is pivotal for the future of the construction industry.
PLAY
Want to Be a Guest Speaker, Sponsor, or Just Have a Question for Us? Fill In the Form!